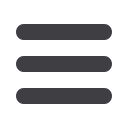

Functional Safety 2014
4
th
– 5
th
November 2014
Copyright © 2014 by Cenbee Bullock PFS Consulting Ltd
Page 13 of 14
Typical examples of some of the human errors during installation and testing are:
i.
Mis-calibration of the instrument such as a level/pressure transmitter;
ii.
Forgetting to re-open and lock the block valves under a relief valve after maintenance and
before the relief valve is returned to normal service;
iii.
Leaving the transmitter/sensor root valve closed causing an unsafe failure;
iv.
Leaving the entire safety instrumented function in by-pass mode after maintenance or after
some other human intervention (such as an unintended error or as a necessity during start-
up)
Statistics from the Process Improvement Institute shows that Probability of Human Error (PHE) varies
from 0.1 to 0.001 depending on the industry and the control of human factors. For example:
i.
PHE = 0.01 to 0.04 for a relief valve being returned to normal operation after maintenance
due to leaving the block valves in the by-pass position;
ii.
PHE = 0.2 while working 30 days of 12 hour shifts during a refinery shut down (In some
countries, there are now restrictions for maximum of 12 days shifts)
Below are some of the recommendations for minimising systematic human failures:
For installation and testing:
i.
Include a test override switch as part of the safety instrumented function;
ii.
Include position switch/indicators on the by-pass block valves;
iii.
Consider the use of an alarm to indicate an active by-pass;
iv.
Apply the two man rule for routine tasks and safety critical activities;
v.
Enforce the use of Installation or Testing procedures;
vi.
Where modification takes place, the system should be re-tested to ensure consistency with
the requirements;
For Testing Procedures:
i.
Be accurate and complete;
ii.
Be clear and concise with an appropriate level of detail (Too detailed and it may be hard to
follow; too little information and it may be difficult to carry out the task correctly);
iii.
Identify any hazards;
iv.
State necessary precautions for hazards;
v.
Reflect how tasks are actually carried out;
vi.
Ensure Procedures are accessible;
vii.
Use consistent terminology;
viii.
Use an appropriate format;
ix.
Use familiar language;
x.
Promote ownership by users;
xi.
Be current and up to date;
xii.
Be supported by training;
Conclusion
There are various reasons for systematic failures; some are inevitable but some may be avoidable.
Outcomes from various studies concluded that a large percentage of accidents were contributed to