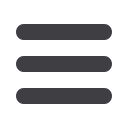

·
Preventative maintenance is a series of routine and planned operations to ensure the functional
safety performance of the SIS is maintained throughout its operational life
·
Corrective maintenance is a process implemented in response to failures and anomalies of the
SIS to restore the functional safety performance of the SIS throughout its operational life
Recent high profile incidents and accidents within the process Industries has brought into sharp focus
the need for Asset Operators to effectively maintain, operate and seek ways to continually improve their
basis of safety whilst managing the heavily regulated and stakeholder expectations of this sector.
Operationally, the process dynamics are changing rapidly on an increasing frequency as process
pressure and temperatures now widely differ across many different assets. With increasing
interconnectivity of the operational platforms with respect to the basis of safe operation, this brings
further challenges for the sustainable management of the asset base.
In addition competitive pressures are such that the industry continues to face greater financial, resource
capture (deep water recovery) and competence issues in meeting the challenge of change. This in itself
has meant that asset management programmes continue to prolong the longevity of the existing asset
base that is already well past the original design life and so the ever increasing impact of delivering
successful O&M.
Today, the use of programmable control systems to implement safety functions is now a common
practice within the Process Industries and Functional Safety Management is achieved by established
IEC 61508 and IEC 61511 Standards. However, for over 30 years, protection and mitigation systems
have been installed on high hazard facilities comprising and including Emergency Shutdown Systems,
Fire & Gas Systems, Boiler Management Systems, etc. These safety related (legacy) systems provide
an essential layer of protection when the plant and equipment experience operational disturbances
which can potentially go out of control leading to an incident.
It therefore follows that the advent of an SIS onto a manufacturing facility is a critical protection system.
During the design and engineering phase, the individual SIF theoretical Safety Integrity Level is
achieved based on certain design assumptions in order to predict the performance of the SIF.
As such, the intended operating conditions will affect these baseline design assumptions and therefore
the eventual SIF safety integrity. Periodic maintenance and proof testing is required to be implemented
as a key specification requirement so as to ensure the continued and demonstrable integrity of each
SIF post commissioning. Therefore competent persons, organizations and supporting management
procedures are necessary to ensure that the system complies with industry good practices and
local/international standards.
The IEC 61511 safety lifecycle approach requires, that appropriate competency is applied in each
phases of the safety lifecycle and this need to be consistently applied using an auditable functional
safety management system. So within the O&M safety lifecycle phases, how can an operator who is
challenged with maintaining process safety and maintaining aggressive production targets actually
implement and monitor a verification and proof testing program? Not performing Functional Safety
maintenance and individual SIF proof testing is simply not an option.
1.3. Effective O&M Practices and what is important for success?
For those safety related systems that have been well managed and maintained (or conversely those
that have not) and thus performed as expected with either good or poor reliability and availability over