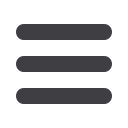

Alumina - 99.8% Aluminum Oxide
Alumina has a maximum service temperature of
3450°F (1900°C)
in both oxidizing and reducing atmospheres. Alumina is considered to
have better mechanical strength (twice the tensile strength of Mullite) and chemical resistance than Mullite. Alumina tubes also have excellent
abrasion resistance. Secondary metal tubes can be added for additional protection from mechanical damage. Alumina tubes are considered
gas tight so they make excellent primary protection tubes. All tubes, which are used in horizontal installations and at elevated temperatures,
should be supported. Alumina tubes can be used for primary and secondary protection tubes on noble metal (platinum based) thermocouples.
Since they have a very low silica content, they will not contaminate platinum elements above 2200°F (1200°C) as a Mullite protection tube.
Alumina tubes should be supported horizontally over 2600°F (1427°C).
Mullite Porcelain - 63.5% Aluminum Oxide, Balance Silicon Dioxide
Mullite has a maximum service temperature of
2900°F (1590°C)
. It is considered to be better than Alumina for thermal shock resistance.
Mullite tube should be used with care, since they have poor mechanical shock resistance. Secondary metal tubes can be added for protection
from mechanical damage. Mullite tubes are considered gas tight at higher temperatures. All tubes which are used in horizontal installations and
at elevated temperatures, should be supported. Mullite tube should not be used for primary protection tubes on noble metal (platinum based)
thermocouples if the temperature will exceed 2200°F (1200°C). Above these temperatures the silica in the Mullite can contaminate the platinum
element if there is not enough air circulation in the tube. Mullite tubes should be supported horizontally over 2100°F (1149°C).
Zirconia - 89.5% Zirconia, 10.5% Yttria
Zirconia has a maximum service temperature of
4172°F (2300°C)
in oxidizing, reducing, and vacuum environments. This material is Yttria
(10.5%) stabilized. Zirconia is chemically inert and has excellent corrosion resistance. Zirconia tubes should not be used in contact with
Alumina above 1112°F (600°C). Zirconia is gas tight, but above 1112°F (600°C) Oxygen will permeate through its structure. To prevent
thermal shock, heat or cool at a rate less than 302°F (150°C) per hour. Zirconia tubes should not be used in sulfur atmospheres or in acids.
Plain End
Inches
Millimeters
Tolerances
Mounting
Alumina
Mullite
Zirconia
O.D.
I.D.
O.D.
I.D.
None
O.D. and
Length
1
AP03-*
AP04-*
AP05-*
AP06-*
AP07-*
AP08-*
AP11-*
AP12-*
AP14-*
AP16-*
AP18-*
AP20-*
AP30-*
P03-*
P04-*
P05-*
P06-*
P07-*
P08-*
P11-*
P12-*
P14-*
P16-*
P18-*
P20-*
P30-*
ZP04-*
ZP06-*
ZP07-*
ZP08-*
ZP11-*
ZP12-*
ZP14-*
ZP16-*
ZP18-*
ZP20-*
ZP30-*
3/16
1/4
5/16
3/8
7/16
1/2
11/16
3/4
7/8
1
1 1/8
1 1/4
1 7/8
1/8
5/32
3/16
1/4
5/16
3/8
7/16
1/2
5/8
3/4
7/8
1
1 5/8
4.8
6.4
7.9
9.5
11.1
12.7
17.5
19.1
22.2
25.4
28.6
31.8
47.6
3.2
4.0
4.8
6.4
8.0
9.5
11.1
12.7
15.9
19.1
22.2
25.4
41.3
None
O.D.
± 5%
or .025”
Length
± .062”
2
Tubes Open Both Ends (OBE)
Tubes may be ordered with Both Ends Open by adding “
OBE
” to the part number before the length. Normally stock
closed end lengths of multiples of 6 inches starting at 12 inches are cut off making the tube slightly shorter, which in most
applications is not a problem (there is a cutting charge).
Common cuts are: 3/8” = 1/2 11/16” = 1/2” 1/2” = 1/2” 1” = 1” 1 1/4” = 1” 1 3/4” = 1 1/2”.
For example
a P11-12 would be cut to P11-OBE-11 1/2. However, an actual 12 inch OBE can be made by cutting down
the next standard longer length (18 inches) but it would add additional material cost (5 1/2 inches) for the 1/2 inch lost.
Tubes with mountings on one end can also be open both ends.
Example:
P16F-OBE-17.
*
Ceramic Protection Tubes - Alumina, Mullite, and Zirconia
Page 104
Phone: 617.527.4385 Fax: 617.964.3746 Email:
sales@asrichards.com