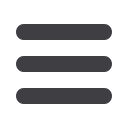

U. K. B. G. GUIDE TO DRINKS
Secondly, the slightly imperfect leaf is taken as an inside
wrapper for this "filler"; this is called the "binder"
Thirdly, the finely textured,"shadegrown leaf of first
class appearance is selected as the outside wrapper .
For its journey to the manufacturer, the leaf is packed
under pressure in hogsheads in which the slow fermentation
process continues. Several years may elapse before it is
ready to be made into cigars.
The Manufacture of Cigars
The"wrapper"of a cigar may not come from the same
country as the "filler ". Many with a Jamaican filling,
for example, may have a "wrapper from Havana so
that they are indistinguishable in appearance from the all-
Havana cigar. Because leaf varies in quality, aroma and
strength, the blending of different leaves is a vital stage in
all tobacco manufacture.
, , ,
The very best cigars are still made by hand and great skill
is required to roll them in a uniform size. After the stem
of the leaf has been removed,the cut filler is laid on the
"binder" and skilfully rolled into a "bunch" of the
approximate length, thickness and shape for the particular
type of cigar. The"wrapper", which is carefully selected
for its appearance, flavour and burning qualities, begins at
the lighting end and is rolled over the"binder"so that
the small veins run lengthwise ; it is tapered off at the
head of the cigar and retained by a tasteless gum.
In some cigar factories the "bunch is formed by a
mould and is afterwards wrapped by hand. For cheaper
cigars, however, there are machines that not only prepare
the "filler", but automatically apply the "binder" and
"wrapper"and produce some 800 finished cigars in every
hour.
Colour, Shape and Size
After - selection and grading, some cigars are tied in
bundles with a silk ribbon, but the majority are still packed
in rows in wooden boxes, the best of which are of cedar
wood. The colour of the leaf is classified by letters which
are marked on the side or bottom of the box as follows:—
258