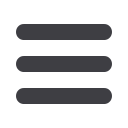

8/26
8
Abrasives
The abrasive grain consists of a precisely arranged, three-dimensional
structure of tiny mineral particles In use new abrasive particle layers are
exposed continuously. Once the tape is half used, about 85 % of the
abrasive particles are still available.
This produces a smooth, reproducible surface. Trizact™ abrasives are
therefore intrinsically suited to finishing and have, compared to
conventional abrasives, a much longer life and are more economical.
Products with Trizact™ abrasive grain:
Abrasive sleeves for use on burnishing machines
Ç
8/59
Trizact™
On grinding small corners of the ceramic sintered grain break off. The
resulting micro-breaks in the grain make sharp edges. This process
repeats itself during the entire grinding operation.
This self-sharpening effect increases its life span considerably. Even
with high temperatures and usage the Cubitron™ microstructures retain
their hardness and cutting action. So it is ideal for grinding stainless
steel, titanium and heat-sensitive nickel alloys.
Products with Cubitron™ abrasive grain:
Hookit™ Velcro-grinding discs
Ç
8/31
ROLOC™ grinding discs from
Ç
8/36
bristle-discs
Ç
8/38 and
Ç
8/46
abrasive sleeves for use on burnishing machines
Ç
8/59
Cubitron™
The individual grains of ceramic Cubitron™ II abrasives are precisely-shaped, uniform in size and arranged at
right angles in the form of small triangles. Naturally Cubitron™ II has the self-sharpening effect of Cubitron™.
Cubitron™ II
Conventional ceramic grain
Cubitron™ II-grit
Different in size and shape as well
as unevenly distributed. The result
is the abrasive's shorter life span
as well as stress fractures and
discolouration of the material:
Precision-shaped, uniform grin-
ding grains, evenly distributed and
symmetrically aligned. The result is
maximum removal rate, a perfect
surface finish, a quicker, cooler
grind, as well as less material
distortion:
The higher deburring of Cubitron™ II-abrasives benefit all metal-working operations, for example: steel construction, container construction,
welding companies, foundries and forges, that use angle grinders and belt sanders for more removal.
Typical applications are:
• Weld preparation/deburring, cast machining
Quicker deburring and finishing that often needs no further
machining and shortens processing time.
• Chamfering before welding
Quicker grinding processes compared to conventional grinding
products and a longer life span.
• General removal work
Universal on steel, tool steel and non-ferrous metals:
All removal work is faster, lighter and gives a smoother finish.
Benefits:
• Higher, smoother removal
• Up to 40 % time saving potential
• 2 to 7 times longer life (depending on the application process)
• Shorter tooling time due to savings on disc changes
• Less pressure means greater comfort for the user
• Less dust and heat development
Products with Cubitron™ II abrasives:
Fibre grinding discs for steel and stainless steel
Ç
5/133
Special abrasive from 3M
1334