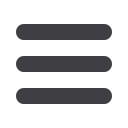

2 0
T H E M A G A Z I N E F O R T H E U K O F F S H O R E O I L A N D G A S I N D U S T R Y
“People know they can now make a
direct contribution to maintenance
optimisation. The technicians can raise
queries on procedures or challenge the
validity of tasks. Those are subject to
a swift onshore review and approval
process and, where appropriate,
change is implemented.”
The programme is also creating
opportunities for technicians to upskill
to perform tasks previously undertaken
by vendors. Maintenance strategy
lead Kevin Bruce notes that “once
people understood why the review was
necessary, and it became clear that we
were doing it for all the right reasons,
there was great buy-in. Every day we see
the maintenance numbers trending in
the right direction so it’s good to see the
hard work paying off.”
Rigorous induction training is now also
given to senior offshore maintenance
personnel. “A great deal of effort went
into ensuring they understood the
context; that they know they have a good
onshore team behind them; and know
what is expected of them,” explains
Stuart. “They’ve been excellent in
cascading those principles to the wider
offshore teams.”
Smart thinking
What started as a pure safety initiative
has ended up adding broader value by
driving smarter operations during the
oil price downturn and beyond.
“If you think of the reliability of your
own car, the same principles apply,”
asserts Trevor. “If you want your car to
start every morning and to run well,
for as long as possible, you look after it
and have it serviced and MOT’d.
“If you get an advisory note for your
car, it might cost a few pounds to get it
repaired there and then. If you don’t,
it might end up being fixed at the
“
MAINTENANCE IMPROVEMENT PLAN
– the review and the results
New onshore and offshore
maintenance teams
created, supporting each of
TAQA’s five assets
Accountability and
ownership for maintenance
delivery brought in-house
14,000 individual preventative
maintenance tasks
(a commitment of about
140,000 man-hours annually)
are being reviewed
130,000 pieces
of information
are being verified
Overdue
safety-critical
maintenance now
consistently
maintained at zero
Non-safety critical
maintenance backlog has
more than halved
Asset reliability improved
from 70 per cent
in 2013 to about
87 per cent last year
Production and
maintenance
working as one collective
operations team
½
TAQA
Cultural change has come about through the
reorganisation. People know they can now make a
direct contribution to maintenance optimisation.
”
roadside and costing an awful
lot more.”
And with many members of the
new-look offshore maintenance teams
recruited from production roles, it’s
changing the nature of asset operations.
“We’re no longer working as separate
entities, with the production team
responsible for the operation of
equipment and the maintenance
team responsible for its upkeep,”
says Cormorant Alpha maintenance
supervisor Gavin Christie.
“We’re working as one collective
operations team, setting out repair
priorities and taking equipment down
on a planned basis for all departments
to work on. Previously, this would have
been completed by teams in isolation,
causing increased downtime and a
reduction in performance levels.”