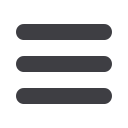

C
oating,
J
acketing & Galvanizing Technology
J
anuary
2008
www.read-tpt.com92
›
Metallisation, UK, is the designer and
manufacturer of groundbreaking thermal
spray units used across the globe. The
company’s metal spray equipment for anti-
corrosion and engineering applications
have been continually developed to meet
the requirements of the industry.
Working with Aston University, Metallisation
has developed a pioneering high velocity
oxy-fuel (HVOF) spray system, the Met
Jet 4. The HVOF system sprays materials
through the combustion of oxygen and
kerosene in a chamber, which produces a
high-speed stream of hot gas at about 2km
per second into which coating material in
powder form is introduced.
This stream of fast-moving powder
– moving at speeds of 800m per second –
produces a dense coating that is particularly
well suited to extreme applications.
Around 5,000 units produced by
Metallisation are in current use around.
Typical uses for Metallisation products
include tube and pipe coating and
spraying protective coatings for turbines
and structural steelwork, such as bridges.
This prevents corrosion and significantly
increase the lifespan of materials. The
company is constantly developing new
equipment to stay ahead of the market.
Dr Terry Lester, managing and technical
director at Metallisation, says:
“Every year
or so we develop a new product through
our design and development team, which
is essential for us to maintain our position
in the industry. More than two thirds of
our products are shipped overseas and
markets with extreme weather conditions
are our key markets.”
“One of the challenges with HVOF is that the
quality of kerosene varies around the world,
depending on how it is produced in different
countries. In doing some research on this,
we joined up with Aston University, through
the Knowledge Transfer Partnership, which
enabled us to secure the services of Ben
Hawkins, an engineering graduate who
helped us develop alternative fuels.”
“Ultimately, this has led to the production
of a spray gun that offers substantial
technological quality and commercial
benefits to both Metallisation and our
customers.”
Metallisation
– UK
Fax
: +44 1384 237 196
:
sales@metallisation.comWebsite
:
www.metallisation.comLatest delivery of new in-line galvanizing system
Superior Technologies Inc has recently signed a contract to supply a new state-of-the-art
in-line Zinc Tech™ galvanizing line to International Tube & Conduit Co Ltd, Saudi Arabia.
The mill will produce high quality galvanized tubes (as well as squares/rectangles) in the
diameter range of 18mm to
76.2mm with a maximum wall
thickness of 4.0mm.
This will be the first in-line
galvanizing plant for tubular
products in the Middle
East region and will be in
operation by July 2008 at the
King Abdullah Economic City
located in Rabigh.
Mr Pete Chifo Jr, president of
Superior Technologies Inc,
said
“We are very pleased
to work with a progressive
and ambitious new company
in the Middle East. There is no doubt that the benefits that our Zinc Tech™ process
offers will position International Tube & Conduit Co very favourably and give them the
opportunity to ‘re-define’ the standards of galvanized tubular products in the region.”
Superior Technologies Inc
– USA
Fax
: +1 909 364 2322
Website
:
www.superior-tech.netSuperior Technologies Europe Ltd
– UK
Fax
: +44 1344 426626
Website
:
www.st-europe.co.ukInnovation recognised for groundbreaking
thermal spray units
fi
Superior manufacture the state-of-the-art in-line Zinc Tech™
galvanizing line