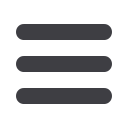

Chemical Technology • November 2015
20
Rethinking
automation
W
orkforce shortages and consumer demands
for customised products mean manufacturers
need to rethink their processes, their met-
rics, and even their automation technology strategies.
Take the traditional industrial robot, for example. Fast
and efficient, these fixed automation solutions deliver the
speed, payloads and mechanical repeatability needed for
high-volume, low-mix environments. Although they have
obvious advantages, they have very real disadvantages for
manufacturers with lower-volume, higher-mix environments.
While fast and precise, high speed robots are also fixed,
expensive, and inflexible.
To meet these unmet needs, a new breed of automa-
tion has emerged that provides an exciting alternative to
fixed automation. This new category is called ‘collaborative
robotics’, and it’s changing what’s possible for manufactur-
ers of all sizes.
This new class of robot has several distinct advantages
over its fixed industrial counterparts, allowing it to:
• Work safely side-by-side with humans
• Perform the simple, repetitive tasks that in the past were
difficult and expensive to automate
• Allow anyone on the factory floor to quickly train it without
needing any programming knowledge
• Moveable to enable quick deployment and changeover
• Interact with its human co-workers and adapt ‘on the fly’
to changes in its environment
• Be incredibly affordable.
• If that sounds too good to be true, then it’s time to rethink
your idea of production robots.
Baxter: Collaborative, and more
Within the automation industry, the term ‘collaborative’ is
used to define robots that can operate safely outside of
a cage. But, to be truly collaborative, a robot must have
the ability to work safely side-by-side with humans, adapt
to changes in its environment, and interact with the very
people it works beside.
Meet Baxter
Built from the ground up to address the challenges of to-
day’s manufacturers, Baxter is a new breed of collaborative
robot that integrates safety, flexibility and interactivity. A
smart, collaborative robot unlike any other, Baxter is:
• Flexible enough to fit into humanworkspaces.
With traditional
and other ‘cage-free’ robots, any slight misalignment can
wreak havoc on a production line. Baxter is different. With
its integrated Robot Positioning System™ and cameras,
Baxter responds intelligently to changing workforce condi-
tions, whether that’s stopping when coming into contact
with a person or adapting to a table being bumped out of
alignment. Traditional robots require building expensive
work cells. Baxter works with existing workspaces and
fixtures designed for human hands by ‘feeling’ its way
into a tight fixture.
• Programmable
‘
on the fly
’
.
Traditional robots require weeks
of programming by highly skilled engineers. With Baxter,
factory employees ‘train’ the robot by moving its arms and
pressing a few buttons. Baxter performs the set task and
then can be redeployed for another task.
• Continuously innovative.
Traditional robots are dumb and
inflexible. They perform the same task repeatedly until
The automated factory environment was
envisioned and built decades ago to meet
the needs of manufacturers producing high
volumes of mass-produced products. Today,
unprecedented change is taking place.