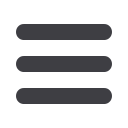

UPM Annual Report 2014
UPM Annual Report 2014
49
50
CONTENTS
UNTIL THE END
OF ITS LIFECYCLE
UPM’s new product ELURIT is
another excellent example of
circular economy: how to prolong
the lifecycle of raw materials by
creating innovative products from
waste. The product is made of fly
ash that comes from the thermal
recovery of the biogenic waste
materials.
ELURIT is the result of research
and development work conducted
at the UPM Schongau mill in
Germany. It will bring about
other economic and environmen-
tal benefits since the use of fly
ash significantly decreases landfill
quantities and disposal costs.
Read more:
www.upm.com/responsibility
The majority of UPM’s production sites, as well as
its wood sourcing operations, are covered by envi-
ronmental, quality and occupational health and
safety systems which are certified in accordance
with the ISO 9001, ISO 14001 and OHSAS 18001
standards.
UPM has certified all its European pulp and
paper mills, the UPM Fray Bentos pulp mill in
Uruguay, and the UPM Changshu paper mill in
China in accordance with the EU Eco-Manage-
ment and Audit Scheme (EMAS). EMAS requires
participants to have an Environmental Manage-
ment System and to publish a third-party verified
Environmental Statement, which increases the
credibility and reliability of environmental data.
UPM has participated in EMAS for 20 years.
UPM products have been granted several ecola-
bels, such as the EU Ecolabel, the German Blue
Angel label and the PEFC and FSC forest certifica-
tion labels.
UPM is the largest producer of EU Ecolabelled
newsprint, graphic and office papers. Ecolabels
demonstrate that UPM’s products meet the envi-
ronmental performance criteria expected by third
parties. Read more about the EU Ecolabel for
converted paper products on the right.
Ecodesign: part of product
development
UPM businesses have adopted an ecodesign
approach in their product development, which
means the systematic integration of environmental
aspects into product design at an early stage, cover-
ing the whole lifecycle. Some examples of UPM’s
ecodesign:
- New UPM Valor publication paper
- Thermoformable UPM Grada wood
material
- UPM BioVerno renewable diesel
- The UPM Biofore Concept Car
UPM’s aim is to deliver “More with Biofore”
by continuously reducing the environmental
impact of its products over the whole lifecycle. For
this ambitious goal to be achieved, resource effi-
ciency needs to play a key role in all company
operations.
Product safety is an important part of product
stewardship and provides customers with products
that are safe to use and environmentally sound.
UPM’s products are manufactured from renewable,
biodegradable and recyclable raw materials.
Yesterday’s waste is today’s
raw material
Nearly all organic production residues, including
bark and wood residues, as well as fibre-contain-
ing solids from deinking and effluent treatment,
are used in energy generation at mill sites. Today,
approximately 90% of UPM’s production waste
is reused or recycled.
Ash resulting from bioenergy production
forms the most significant proportion of UPM’s
solid waste. Ash is used on a large scale in applica-
tions ranging from landscaping to road building.
UPM has developed innovative ways to reduce
its own waste or residues and reuse waste in new
products. See the picture on the right.
UPM is also the world’s largest user of recov-
ered paper for the production of graphic paper,
consuming 3.4 million tonnes of recovered paper
in 2014. At UPM, 35% of all fibre used in UPM’s
paper production is recycled fibre.
By 2020, UPM aims to reduce the amount
of its solid waste sent to landfill by 40% compared
with the 2008 level. The reduction target was
increased in 2012 because of the good progress
made.
UPM is committed to maximising the reuse of
materials and minimising the generation of waste.
In 2014, 76% (75%) of UPM’s overall sales of
paper, chemical pulp, plywood and timber
products was ecolabelled. This figure includes
FSC, PEFC and EU Ecolabels, and national
ecolabels. By 2020, UPM aims to increase the
share of ecolabelled products by 25%
compared with the 2008 level.
HAMELIN GROUP ADOPTS EU ECOLABEL
FOR CONVERTED PAPER PRODUCTS
The European Union has extended the scope of the EU Ecolabel to
cover converted paper products. It is the very first official EU Ecolabel
criteria created by an external consortium. Hamelin Group, together
with UPM, played a key role in developing the new criteria.
Hamelin Group was the first UPM customer to adopt the EU Ecolabel
for a wide range of its stationery products, such as notebooks and
envelopes.
According to Virginie Ori, Director of Sustainable Development for
Hamelin Group, the new criteria are an excellent opportunity to
highlight the best practices of the company.
“Products with the EU Ecolabel have a reduced environmental impact
throughout their lifecycle, from the sourcing of raw materials to the
production, use and recyclability of the product at the end of its life.”
“So we decided to certify all our products that fell within the scope of
the criteria and even included the principles in our product ecodesign
processes from a very early stage. Our customers expressed their
interest in the demanding criteria, as they responded to their
requirements,” she says.
Read more:
www.upm.com/responsibility250
200
150
100
50
0
14 13 12 11 10 09 08 07 06 05
UPM’s total waste to landfills
1,000 t
The total amount of solid waste
sent to landfill has decreased
over the last ten years by over
30%. However, from 2012
to 2013 the total amount of
waste sent to landfill increased
significantly. This is due to the
fact that former reuse possibilities
for ash ceased at one of UPM’s
paper mills. In 2014, new
methods of reuse were
established, with further options
for reuse still being investigated.
UPM’s construction
product Cinerit is
made of fly ash from
the thermal recovery
of biogenic waste
materials.
UPM’s new product
ELURIT, made of fly
ash, can be used
at the pulping and
bleaching stages of
the papermaking
processes.
UPM is the world’s
largest user of
recovered paper
for the production
of graphic papers.
UPM ProFi composite
products are made
from the surplus paper
and plastic left over
from the production
of self-adhesive label
materials.
UPM’s renewable
diesel, UPM Bio-
Verno, is produced
from crude tall oil,
a residue of pulp
production.
Taking care of
the entire lifecycle
FI/28/002
Please collect used
paper for recycling.
Read more on product safety (p. 47),
UPM Valor printing paper (p. 26),
UPM BioVerno renewable diesel (p. 18)
and UPM Biofore Concept Car (p. 32).
UPM's ecolabeled sales
*)
EU Ecolabeled sales
50% (incl. products
with multiple labelling)
Sales without
ecolabels 24 %
Other eco-
labeled sales
26% (FSC,
PEFC, SFI,
German
Blue Angel)
*)
incl. Paper, Pulp,
Plywood, Timber and ProFi
35%
OF ALL FIBRE USED IN PAPER
PRODUCTION IS RECYCLED.
RESPONSIBILITY 45–59