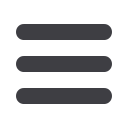

N
ovember
2008
www.read-tpt.com100
›
C
utting,
S
awing &
P
rofiling
T
echnology
Trumpf, Germany, has supplied two state-
of-the-art CNC laser cutting machines to
Savekers, a UK-based OEM that supplies
an innovative range of architectural
metalwork items to a host of industries.
These machines have led to benefits that
include an impressive reduction in cycle
times of 50-60 per cent on average.
Savekers architectural metalwork range
includes sliding door and window track
products, retail systems, shelving systems,
pedestrian guidance and barriers, and
leisure products. Manufactured largely from
tube, plate and sheet steel, all production
operations (with the exception of powder
coating) are conducted onsite.
Until recently Savekers had no laser cutting
facility for tube and relied on an ageing
waterjet profiling machine for its plate work.
For laser cutting tube and profiles, the
Trumpf TruLaser Tube 5000 is an automatic
and flexible machining system.
It can process tube up to 6,500mm in
length with wall thickness up to 6.4mm
(mild steel). The machine is available with
a loading unit and part removal station.
The TruLaser Tube 5000 makes it possible
to cut tubes and profiles into sections in a
single setup. It also makes it possible to
produce recesses and
contours with the laser,
an attribute exploited
widely by Savekers
for nearly all of its
products.
“Whereas we previously
bought
pre-slotted
tube we can now
manufacture slots of the
desired length and in
the exact position required by each customer,”
says Saveker’s chairman Mr Martin Saveker.
“Previously we had to offer ‘universal’ versions
of our slotted tubular products.”
Mr Saveker says that
speed was the major
consideration
behind
seeking new flatbed
profiling capability. Having
already decided to buy
the Trumpf TruLaser Tube
5000, another model was
selected – the Trumpf
TruLaser 2525.
“We can cut at 200mm/
min using our existing
waterjet facility, however
the TruLaser 2525 can
profile at 20,000mm/min
for some jobs,”
says Mr
Saveker.
With travels of 2,500mm, 1,250mm and
115mm in X, Y and Z respectively, the
Trumpf TruLaser 2525 can cut up 20mm
thick mild steel, 15mm stainless steel and
10mm aluminium.
Typical Trumpf innovation is applied in the
form of an additional Y-axis integrated in
the motion unit. Unlike the standard Y-axis,
it does not move the complete motion unit
– only the cutting head.
The intelligent application of a double axis
greatly increases the dynamics and reaction
time of the machine and, particularly on
small part geometry, processing time can
be reduced by up to 30 per cent.
Advantages of the TruLaser Tube 5000
have so far included design of more intricate
products, zero tooling requirements,
extensive de-stocking, enhanced cut finish,
and cutting of parts ‘on-the-fly’ from material
that would conventionally be scrap.
“We’ve easily cut 50-60 per cent from cycle
times,”
states Mr Saveker.
Trumpf Group
– Germany
Fax
: +49 7156 303 6115
:
harald.dickertmann@jp.trumpf.comWebsite
:
www.trumpf.comTrumpf Ltd
– UK
Fax
: +1582 399 250
:
sales@uk.trumpf.comLaser machines cut cycle times
by 50-60 per cent
The Trumpf TruLaser Tube 5000 for laser cutting
A test cut part example