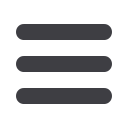

49
N
ovember
2008
www.read-tpt.com›
to its parametric structure. The lineal beams
are either predefined or – if there are single
mounted rolls – each roll and respective
position is defined in specific database
tables.
In order to achieve a correct forming result
it is important to have a smooth strip entry
into the forming cage.
Therefore it is important to optimise both
entry passes as well as the position of
forming and guiding rolls in the forming line.
There are some obvious advantages to
perform a mill setup on the computer
rather than on the mill by practical trials.
These include the possibility to add, edit
process Copra
®
FEA RF 2009. Copra FEA
RF helps the manufacturer to understand
the rollform process, trace reccurring
problems and carry out target-oriented
optimisation.
Due to the fact that rollform technology
is continually developing, data M sees it
as essential to add new possibilities into
the FEA software. The company believes
that this new version has come closer to
reality than any other simulation or analysis
software.
The company has enhanced both the FE
Analysis software and also the renowned
design package Copra RF. One specific
feature to have been improved is the
handling of cage forming methods.
Copra CageForming is a straight forming
method that enables the possibility to
design and model any type of rolling cage.
A cage forming system is a continuous
forming process by groups (beams) of
single simple rolls and additional supporting
outer and inner roll tools.
Copra allows for a modelling of various
types of straight edge forming systems due
from 3″ to 26″ diameter. The company
currently has many international projects in
industries including oil and gas, automotive,
and construction.
Website
:
www.btwcorp.comAt Tube Arabia 2009, data M Software
will present the new version of its finite
element simulation solution for the rollform
A six roll straightener from Bronx/Taylor-Wilson
data M Software
Germany
Copra RF now also supports integrated drawing
dies.