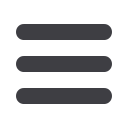

N
ovember
2008
www.read-tpt.com66
›
E
ven exclusive of
the multitude
of polymers that
can be extruded
into plastic tubing,
and of the remarkable
T
ube
E
xtrusion &
D
rawing
T
echnology
‘pultrusion’ process for the production of fibre-
reinforced tubes, extrusion technology is versatile
to an extraordinary degree.
Tubing may be extruded from aluminium, copper, lead
and tin, magnesium, zinc, plain carbon and stainless
steel – even titanium. Magnesium is approximately
as extrudable as aluminium for tubing in avionic and
nuclear applications. Molten lead may be used in place
of billets on vertical extrusion presses.
Hot extrusion or cold extrusion?
Either method yields superb results; and the products are
readily mass-produced and cut to length, economical, and lightweight. Tube extrusion does
it all.
And tube drawing does the rest, also supremely well: sizing and re-sizing, reducing, changing
inside and outside diameters and wall thicknesses, satisfying custom requirements for close
dimensional control and smooth
and ultraclean surfaces. Drawing
is the method of choice for
refinement of the grain structure
and enhancement of the finish.
Tube extrusion or tube drawing?
To judge from the performance
history of these highly evolved
companion processes – as
complementary as any in the tube
making business – the probability
of satisfaction is excellent with
both.
The foam-core pipehead series, from KraussMaffei Berstorff,
includes two twin-screw extruders (see page 68)
Battenfeld supply large-diameter pipe extrusion lines up to 2,000mm in diameter (see page 70)