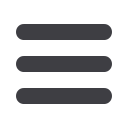

N
ovember
2008
www.read-tpt.com86
›
C
utting,
S
awing &
P
rofiling
T
echnology
cutting opens up new possibilities. All of the
traditional methods of cutting and machining
tubes generate mechanical loads, which in
turn can induce stresses into the materials
and parts being processed.
Laser cutting, however, is a contact free and
highly flexible process. Simple programme
changes enable different parts and profiles
to be produced without the need to perform
any tool changing operations.
materials, ferritic steels such as 1,4509,
1,4520 or even 1,4521 are currently
being used. These steels are often more
economical, but still offer a technically
feasible alternative in many application areas
due to their equal corrosion resistance.
When manufacturing stainless steel tubes,
the process benefits of the laser allow
precise control of the laser parameters and
therefore the energy used to create the
weld, along the full length of the tube.
The laser also offers distinct advantages
when it comes to system availability: the
contact-free CO
2
slab laser system has an
availability of almost 100 per cent, unlike
the traditional TIG-welding process with
its electrodes which have to be replaced
regularly, causing inevitable breaks in
production. In addition to Esta, more than
twenty other companies worldwide have
opted for Rofin’s CO
2
slab lasers combined
with the profile welding system for the
manufacture of stainless steel tubes.
With its integrated gap recognition, the
PWS sensor technology adjusts for the
smallest deviation of the weld seam
position, providing optimum welding results
even under difficult conditions. Rofin states
that laser weld seams are more resilient
than conventionally created weld seams,
which is a distinct advantage when tubes
are to be formed and manipulated following
the welding process.
The benefits of speed and precision are
also apparent in the laser cutting and
profiling of tubes. In instances where
traditional methods such as drilling, milling,
sawing or die cutting reach their limits, laser
Steel tubes are used to produce a vast
array of products including water pipelines,
steel furniture, machine frames and even
the fine tubes of less than 200µm in
diameter used within the medical device
industry.
Thousands of miles of pipeline, tube and
profiles are formed, welded, cut and marked
every day. In many cases, the machines
used for this diverse range of applications
have lasers at the heart of the process.
Rofin, Germany, produces a complete range
of laser sources and solutions, for use in
an increasing number of applications. The
advantages of laser welding are well known
to Esta Rohr, a manufacturing company in
Siegen, Germany.
Esta Rohr produces longitudinal seam
welded, stainless steel pipes on a 3-shift
operation, using a 4.5kW CO
2
slab laser
integrated within a Rofin profile welding
system (PWS).
“
The benefits for us are obvious
,”
commented Mr Sven Pitzer, technical
manager of Esta Rohr. “
Compared to the
traditional TIG-welding process, the laser is
three times as fast. For example, we were
welding tubes with dimensions of 18mm x
1mm with the conventional TIG-machine
at 5.5m/min. By comparison the laser
achieves 16m/min, and it is not the power
of the laser which restricts the speed, but
the subsequent in-line annealing unit.
”
Another important factor for Esta Rohr is
the capability of the profile welding system
to weld both austentitic and ferritic stainless
steels. In addition to the range of austenitic
Lasers in tube manufacture – a well-rounded process
Traditional methods
of cutting and
machining tubes
generate mechanical
loads which can
induce stresses into
the materials
and parts
❱
❱
Laser welding of tubes using the Rofin profile
welding system
(Below) Medical stent production using Rofin’s StarCut tube system; and (below right) a close-up view of a stent