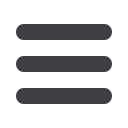

EuroWire – September 2010
36
technology news
Metal tape forming and
welding technology
New induction heating systems
At wire 2010, ATE presented two new induction heating systems to complete its range
of continuous heating systems for the parallel treatment of wires. The new systems are
called IMW and CMW.
The main feature of the IMW system is the simultaneous heating of each wire, even
where they have different diameters, by means of a dedicated inductor fed by the
related frequency converter.
The CMW system is instead designed for a bundle of wires, heated using a single
inductor fed by a single frequency converter.
The advantages of these new systems over traditional systems are in terms of efficiency,
energy consumption, quality and compactness. Applications may include annealing,
stress relieving, brass-diffusion and pre-heating or other industrial processes requested
by the end-user.
ATE Applicazioni TermoElettroniche Srl – Italy
Fax
: +39 0444 406434
:
info@ate.itWebsite
:
www.ate.itRosendahl has broadened
its portfolio to offer welding
and corrugation equipment
for power cable applications
following the demand of
the industry for alternative
solutions, and based on
experience
of
successful
projects in the field of metal
tape forming, welding and
corrugation for high-end RF
cables.
Cable manufacturers require
this technology for products
such as cables for wind farms,
offshore power stations or
cables for submarine appli-
cations. The LV segment also includes a
number of products (oil-pump, shipboard,
signal cables), which use the Rosendahl
technology to improve product properties
or to increase productivity during the
manufacturing process.
Compared to other technologies (alumi-
nium or lead extrusion) the metal tape
forming and welding system has several
advantages. It shows better results for
continuous operation, economic use of
electric power and water, reduced scrap
during production, dimension change and
the possibility of using different metallic
materials for shielding.
Cables produced in this way are said to
demonstrate superior mechanical stability
and water and/or gas tightness.
Technologies developed and optimised
for these applications include:
Optimised formers for various
•
materials
Welding processes – to ensure
•
perfect weld seams with minimal
heat affected zones and best
mechanical properties
High speed corrugators for helical
•
and annular corrugation for copper,
aluminium and stainless steel
For metal shielding by means of smooth
or corrugated aluminium, copper or
stainless steel, Rosendahl offers solutions
for the tape forming, welding and tube
reduction process including adequate
down stream equipment.
Depending on the cable design, space
availability and product mix, Rosendahl
is in the position to serve inline (in
combination with the jacketing process)
and offline solutions.
Rosendahl Maschinen GmbH – Austria
Fax
: +43 3113 5100 59
:
office@rosendahlaustria.comWebsite
:
www.rosendahlaustria.comWelding and corrugation equipment for power cables
▲
▲