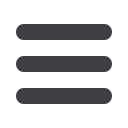

EuroWire – September 2010
69
technical article
During further processing at high tempera-
tures the thickness of the alloy layer that
forms between the base material and
the tin coating of tin-coated BB05xi is
comparable to that of CuFe2P.
Production lines therefore do not have to
be converted to accommodate this new
composite material
(Figure 4).
Moreover, this new alloy is significant as
the tin-plated scrap from the individual
stages of the value chain is directly
recyclable.
A comparison of the metal values BB05xi
and CuFe2P also does not justify the
difference between the costs of indirect
and direct recycling of production and
punching scrap, which in this sector are
usually 20% to 25% of the metal value – a
factor of considerable importance in times
of high and increasing raw material prices.
With a scrap percentage of, for example,
70% the smelting costs can rapidly match
the production costs, casting doubts on
the economic feasibility of the whole
process.
The use of a tin-coated phosphor bronze
is therefore a worthwhile alternative to
tin-coated copper-iron alloys from both an
ecological and an economic point of view
(the additional use of electricity and acid
for the electrolytic treatment of the scrap
is eliminated).
2.2 Development 2
Copper-tin alloys are used for connectors
and components for electronic and
electrical engineering applications as
they have good to very good spring
characteristics, good resistance to electrical
and thermal stress, low stress relaxation
and excellent bendability and solderability.
Usually a small amount of phosphorus is
added to alloys of this type for the purpose
of deoxidation, which is why they are also
referred to as phosphor bronzes.
The properties of this group of alloys
depend mainly on their tin and
phosphorus content, and to a lesser extent
on the other added alloy elements.
By means of suitable processing they can
be adjusted for use in a wide range of
applications.
The many industrial applications for these
alloys range from high quality connectors
and sockets for electronic modules to
electrically conductive contact springs.
In the past “downgrading” was carried
out as an efficient method of selecting
a phosphor bronze. In other words, the
technological properties of a low-alloy
phosphor bronze were adjusted so that
its spring characteristics and processing
properties corresponded to those of the
original high-alloy phosphor bronze. How-
ever, certain constraints had to be taken
into consideration.
The tin and phosphorus content influence
the work hardening behaviour and ductility
of phosphor bronzes to a considerable
extent, and a clear relationship has been
found between the achievable bendability
and the tin content.
Figure 5
shows how increasing the tin
content has a positive influence on the
bendability at constant strength.
Against this background it was logical to
develop a higher-alloy phosphor bronze.
Another reason to do so was the demand
for miniaturisation of connectors, as a
reduction in cross-section reduces the
contact force at constant deflection of the
spring element.
For a defined constant force, therefore, the
spring element has to be redesigned – the
design stress increases accordingly. One
solution for this is the newly developed
alloy BB95, a 10% phosphor bronze.
At a yield stress level Rp0.2 > 720 MPa,
the bendability of BB95 in BW90° R/S is
superior to that of an 8% tin bronze by a
factor of 2.
Depending on the intended application,
BB95 can be hardened to a yield stress
level Rp0.2 of 800 MPa, and the high
strength variety to >950 MPa.
Figure 3
▲
▲
:
Comparison of the relaxation behaviour of CuFe2P and BB05xi
Figure 4
▲
▲
:
Formation of the alloy layer at 180°C after hot-dip tinning
Temperature in ºC
Relaxation in %
Exposure time in h
Alloy layer in µm