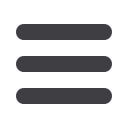

21
CONSTRUCTION WORLD
MAY
2017
Due to the close proximity of the readymix plants to the PwC site,
the batch load size and loading sequences were optimised at 2 m
3
to make sure the mix was homogeneously mixed before it left the
plant. The concrete slump was also maintained strictly at 180 mm
from the plant.
Slip forming the core wall
The building’s core wall, at a height of 118 metres and thickness
of 450 mm, was constructed using an interesting method of
construction – slip forming. This sliding methodology starts with the
assembly of the sliding system at ground level. Concrete is poured
continuously within shutters and the system is lifted incrementally
as concrete is poured, creating a structure without joints.
Reinforcing is then fixed into position as the slide progresses so
as not to slow down the placement of concrete; over 400 tonnes of
reinforcing was used in the core wall.
Working continuously in two 12 hour shifts, the sliding team
comprised at least 62 workers on the slide shutter itself at any one
time. This allowed the core wall to be constructed in 65 days, with
an average of 90 m
3
of concrete placed per day.
Concrete mixes
AfriSam had to design concrete mixes that were both pumpable and
suitable for slip forming, including specialised retarded mixes that
could be continuously pumped up into the moving slide around the
clock. A static pump would pump the concrete into the slide cavities
using a spreader that was fixed to the slide.
Pumping vertically over 100 metres would mean possible high
pump pressures and the need for lubrication within the lines had to
be considered, and steps taken to avoid segregation and blockages.
If the pumping pressure was too high, excessive pressure would be
placed on the mix and this could force segregation of the concrete
(water washing out of the paste) and cause blockages in the pipe.
In addition to this, the pump would be started and stopped for
extended periods when shuttering inserts and reinforcing had to be
installed, with the pump and pipeline full of concrete. Another factor
would be the continuous stop/starting action as the hose was lifted
out of the reinforcing forest and inserted again into its next position;
the reinforcement in the lift shafts would also be very dense. This
highlighted the need for the concrete to remain workable for up to
six hours, long enough for it to pass through the pipeline and be
placed into the structure. A concrete non-return valve was used to
prevent any backflow; opening and closing as the pump worked.
AfriSam incorporated about 30% fly ash in the mixes to increase
the pumpability and slow down the initial setting time. To achieve
this, a combination of three CHRYSO additives was used including
a superplasticiser and retarder which delays the setting time of the
concrete. This provided enough time for concrete to be placed into
the form, around the core wall, and vibrated so the sliding process
could continue.
The concrete would exit the bottom of the slide 10 to 12
hours after casting. It could not be allowed to harden during this
time as this would reduce the ‘slip effect’ and make it difficult to
incrementally lift the sliding system. The concrete supported the
slide platform.
Visible from a 30 km radius, the R1,5-billion PwC Tower will comprise
45 000 m
2
of office space and house 3 500 employees.
Concrete is poured continuously within shutters and the system is lifted
incrementally as concrete is poured, creating a structure without joints.
Grand scale
A total of 6 057 m
3
of concrete was used to construct the core wall.
Concrete is normally placed using a bucket and crane; however, due to the
large quantities of concrete involved, it was decided to pump the concrete
vertically up to the height of 118 metres. When concrete was pumped to
the top of the building, there was 3,5 m
3
of concrete in the pipeline.
→