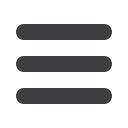

WCN
Issue N° 42
www.iwma.org18
John C Hogg Travel Awards for
wire Düsseldorf 2010
The John C Hogg Travel Award, which the IWMA offers to
trainees, apprentices and students through its Educational
Trust, attracted sixteen applicants for Düsseldorf 2010, of
whom ten have been given an award.
This scholarship gives the recipients a unique opportunity
to visit the world’s largest and most important wire fair,
with travel and two nights accommodation funded by the
IWMA Educational Trust.
Recipients are also invited to the IWMA’s gala dinner during
the wire show, which this year is on Tuesday 13
th
April.
The recipients of the 2010 awards reflect the worldwide
influence of the IWMA coming from India, Canada, and
Europe. As a memento of the occasion each awardee will
receive a commemorative certificate from the Chairman of
the IWMA at a ceremony on the Association booth – 11 D26
– in Hall 11 at 14:30 hours on Wednesday 14
th
April 2010.
Friedrich Kehrer, Messe Düsseldorf’s project director for
the exhibition, will also officiate at the ceremony when he
will present each recipient with a wire catalogue. Messe
Düsseldorf also provides free exhibition entry passes for
each award winner.
Recipients of the 2010 John C Hogg Travel Awards are:
Mr R Killick, Whitelegg Machines Ltd, UK
Mr GT Robinson, XL Technologies Ltd, UK
Ms L Colloca, B & B Compounds, Italy
Mr C S Mantha, Innovites, India
Mr S Thornton, Bar Products and Services Ltd, UK
Mr M Certosini, QED Wirelines Inc, Canada
Mr R Manjunath, Mikrotek Machines Ltd, India
Mr J Coldwell-Horsfall, Webster and Horsfall Ltd, UK
Mr K Nandagoplan, Niehoff, India
Mr O Çinar, ER-Bakir, Turkey
Travel awards for Düsseldorf are just a part of what the
IWMA, through its Educational Trust, does for trainees
in the industry. Scholarships are available for further
education and training and can be awarded to either
individuals or organisations. (
Please see item on page 15
).
Uhing-AVS at Goodyear
Warped metal spools require frequent adjustment of the
traversing width if such spools are to be reused. This
negatively affects the cost efficiency of the production
process and the staff productivity. The automatic winding
width control developed by Joachim Uhing KG GmbH
& Co prevents the formation of undesired bulges and dents
of wires wound in the flange area of spools and relieves the
staff from unproductive monitoring tasks.
A project the company is running in the Luxembourg plant
of tyre manufacturer Goodyear Dunlop demonstrates the
excellent operation of the AVS.
The metal spools on which Goodyear Dunlop winds the
1mm-2mm thick steel tyre cord are used in several locations
of the Colmar-Berg plant. During their service life, some of
the spools change their initial geometry considerably, bent
flanges being the central issue. As a consequence, many of
the traversing systems, even those equipped with sensors,
fail to accordingly correct the winding width and require
manual intervention by operators. As staff spend much time
monitoring the winding processes, more productive tasks
were neglected. This made the plant management search
for other traversing solutions.
Goodyear Dunlop approached Joachim Uhing KG GmbH
& Co. Aiming at providing the tyre manufacturer with
a smooth winding pattern in the reversing area of the
traversing system known to be particularly critical, Uhing
developed the automatic winding width control AVS.
Two sensors monitor the material’s line speed and the spool
speed. When a dent forms at the end of a stroke, the spool
speed slightly increases in relation to the constant material
speed. A third sensor identifies the position of the traversing
system and reports the faulty stroke end to the controller
that accordingly increases the material supply in the dent
area by widening the traversing width at this stroke end until
the flaw has been corrected.
In case of a bulge, the spool speed will decrease along with
the traversing width and consequently the material supply.
This results in an optimum pattern on the spool and ensures
smooth unwinding later on. The Uhing AVS is extremely
unsusceptible to soiling, since it lacks optical sensors, and
can be integrated into existing traversing systems as a
complete system or in parts.
wire Düsseldorf stand: 11B40
Joachim Uhing KG GmbH & Co – Germany
Fax
: +49 4347 90640
:
sales@uhing.comWebsite
:
www.uhing.comA sample configuration of the Uhing AVS
▲
▲