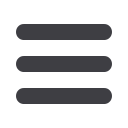

News
Corporate
January 2017
16
www.read-eurowire.comThe Fire Retardant Additives (FRA) business unit, part of the
Huber Engineered Materials division of J M Huber Corporation
(Huber), has announced a 10 per cent capacity expansion of its
Martinal® fine precipitated alumina trihydrate production at its
newly acquired Martinswerk Plant in Bergheim, Germany.
The additional capacity is projected for completion by the
third quarter of 2017. This addition follows a 20 per cent
capacity expansion in precipitated alumina trihydrate just
completed at Huber’s Bauxite, Arkansas, facility in the United
States.
The investment by Huber in additional capacity in Bergheim
commenced only seven months after the February acquisition
of Martinswerk GmbH, including the joint venture interest in
Magnifin Magnesiaprodukte GmbH & Co KG.
Huber is a global leader in the production of fine precipitated
alumina trihydrate and magnesium hydroxide, both
non-halogenated fire retardants. Its FRA business unit has four
manufacturing sites in North America and two in Europe.
J M Huber Corp – USA
Website
:
www.huber.comCapacity expansion for Huber
WILLIAM Hughes, a specialist manufacturer of springs and bent
wire components for the global automotive and aerospace
industries, has invested more than £250,000 in a high technology
twin robot welding cell.
The new welding cell was supplied by Bauromat with Fanuc
robots, all installed at William Hughes’ new UK headquarters in
Stalbridge, Dorset.
The unit features advanced weld monitoring and recording
ensuring that the highest standards of quality and consistency
are maintained for its customers.
“We have been very successful in winning significant new
business from our automotive customers and this has meant
that we needed to increase our production capacity for our
welded seat frame assemblies,” said Emma Burgon, engineering
director.
“The Fanuc twin robot welding cell was the obvious choice as we
already have a number of Fanuc machines within our organisation
and are familiar with their programming and operation.
“The twin robot version more than halves the time required for
the welding process and this has provided a significant increase
in our manufacturing capacity.”
The welding cell is in operation 24 hours a day during the
working week and is currently being used for the bulk
manufacture of seat frame backs for an SUV. This particular
assembly has 56 welds and uses 25 wires.
As well as the improved quality and consistency of the finished
product provided by the twin robot cell, the welding process is
much quicker, enabling parts to be produced in just 1 minute 40
seconds compared with 3 minutes 45 seconds previously.
Furthermore, to ensure throughput speed is maximised, the
weld jigs are all designed by William Hughes engineers using
the latest CAD software and manufactured using CNC milling
machines.
This recent investment in the latest manufacturing technology
continues William Hughes’ programme of continued growth
which includes the opening in October 2014 of a new
87,000ft
2
factory at its UK base in Stalbridge.
The company also continues to invest in the growth of its
manufacturing facility in Bulgaria, which is servicing the needs
of its European customers.
William Hughes Ltd – UK
Website
:
www.wmhughes.co.uk£250,000 investment in the latest technology
▲
▲
The twin robot welding cell