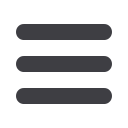

The Importance of Functional Safety Assessment and its Application
Page
3
of
12
1. Introduction
Organisations that operate and maintain a Safety Instrumented System (SIS) and whom wish to claim
compliance to the IEC safety standards shall ensure that the design, engineering, verification,
validation, installation, commissioning, operation and maintenance of the system safety lifecycle shall
comply with the detailed clauses / requirements as found within IEC 61508 and IEC 61511.
This is achieved by assessing the appropriate evidence provided and thereby applying an expert
judgement on whether functional safety is achieved or maintained. This process of analysis is defined
as the Functional Safety Assessment (FSA).
Organisations involved in the operation and maintenance stage of the safety lifecycle of the SIS shall
ensure that FSAs are periodically conducted in order to review the SIS performance, with more
emphasis for when the SIS undergoes any modification.
This paper provides an insight into the FSA process, its importance, and the practical application of
how this can be undertaken and the associated benefits of conducting the Functional Safety
Assessment.
2. Drivers for FSA
Process safety is of paramount importance for any process industry and is one of the important
factors in the operation of process plant. Based on the process hazard analysis and the subsequent
allocation of differing levels / layers of protection identified, implementation of these protection layers
attributes to process safety.
Designing and engineering the protection systems in accordance with the safety requirements
specification and the requirements of the functional safety standards plays a major role in establishing
the necessary risk reduction for operation of the plant.
The designed system shall be installed and commissioned in alignment with the requirements of the
IEC standards and will then need to be validated for the operational requirements.
Every protection system will need to be operated and maintained in-line with the standard operating
procedures of the plant. This is typically based on the safety requirements specification and the
requirements of the functional safety standards covering the operation and maintenance phases of
the lifecycle.
Experience shows that there may be significant gaps in implementing a robust lifecycle management
process to ensure that the functional safety requirements have been met at every phase of the
lifecycle and that there is no compromise.
The “Out of Control” publication from the Health and Safety Executive in U.K. identifies that more than
60% of the failures can be built into the safety related system before it is taken into service. A
significant contributor for these failures is the systematic failures as opposed to the random hardware
failures. Following a robust Functional Safety Management System (FSMS) for design and
engineering of a SIS ensures initial compliance to the functional safety standards, however if the SIS
capabilities are not verified or assessed periodically, then the failures tend to be submerged within
and will be transferred from the design phase to the operation & maintenance phase.