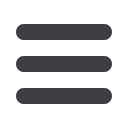

CAPITAL EQUIPMENT NEWS
JULY 2017
36
The worldwide trend across all industries
to reduce dust in the working environment
is underpinned by the dangers when
personnel are exposed to excessive dust.
The need is no different in the mining
sector where large volumes of material are
conveyed vast distances, and moved from
one conveyor system to the next before
reaching its final destination.
Mark Baller, MD of Weba Chute
Systems, says that the company’s custom
engineered transfer systems have played
a major role in addressing the dust issue
for many years on mines across the world.
Baller says that Weba Chute Systems
provides a viable solution to this potentially
hazardous situation where excessive dust,
especially fines, can be both hazardous
to workers’ health and create greater
abrasion to wearing parts, resulting in
increased maintenance.
“Majority of the dust generated in the
mining and minerals beneficiation industries
is created during the transfer of material,
and it is not enough to merely install
extractive equipment,” he explains. “It is
essential to identify the actual source of the
dust problem and engineer an appropriate
transfer system to minimise the dust.”
Once this has been done, less powerful
dust extraction equipment will be needed
with consequent savings in both capital
equipment expenditure and energy
consumption.
By controlling the fall of material in the
transfer point, material degradation can
be dramatically decreased by up to 80%,
with a resultant decrease in dust and noise
emission.
“Obviously the higher the drop, the
greater the potential for more dust to
be created. The Weba Chute System is
configured to control the direction, flow
and velocity of the calculated volume and
type of material processed in a particular
application. This absolute control of
material has a marked effect on impact
resulting in significantly lower amounts
of fines and dust being created,” he
adds.
b
MINING NEWS
Mining may not dominate the economic landscape as it once did, still it
remains a tremendously significant player. The mining industry accounts
for 20% of all investment in South Africa and generates R441 billion in
expenditure annually, of which R407 billion is spent locally.
Despite its importance, the mining sector is facing severe pressure on
various fronts, including costs, environmental liability and the lack of a
cohesive strategy in terms of minerals demanded by the future “green”
economy. Converting these challenges into opportunities was the theme of
the Sustainability and Mining Seminar at Sustainability Week 2017, which
took place on June 14, 2017 at the CSIR International Convention Centre, in
Tshwane.
“On a global front, mining operations face severe economic and financial
challenges, including escalating costs, reduction in resources, labour availability
and effective labour utilisation. The gold mining industry, particularly in South
Africa, is facing gold price volatility, where rising costs, decreasing commodity
prices, lower ore grades and labour issues are squeezing profit margins and
ultimately affecting competitiveness in the industry. This is a catch-22 in terms
of the growth of the South African industry, as it makes strategic planning very
difficult,” says Tshego Motsoenyane, chief operating officer at Ncamiso Mining.
“The sustainability of mining in South Africa is heavily affected by the
social implications of widespread labour unrest which imply a lack of trust
and transparency between the mining companies and the employees. The
company and employee goal alignment issues affect productivity and profit
yield resulting in further wage issues. If these issues are not addressed, the
sustainability of the industry is seriously compromised.”
The message is clear: by sustaining the planet and the people, mining
companies can sustain their profits – a virtuous circle for a sector under
pressure.
b
Creating a virtuous circle for mining
South African mining companies must
transform to survive
Struggling with commodity prices, declining ore grade
and operational challenges, South African miners have
no choice but to focus on creating operational excellence
to buffer against declining margins. Creating operations
By controlling the fall of material in the transfer point, material degradation can be dramatically
decreased by up to 80%, with a resultant decrease in dust and noise emission.
Weba Chute Systems assists in dust reduction at mines
Companies must enable processes and decision-making
beyond the operational siloes endemic within most mining
companies.