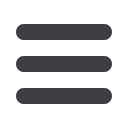

CAPITAL EQUIPMENT NEWS
JULY 2017
2
EDITOR'S COMMENT
L
ast year the global mining sector
was in dire straits, on the back of
downward commodity prices. With
mining being a money spinner for most
African economies, investments into
infrastructure development activities also
dried out, meaning both construction and
mining contractors felt the full brunt of
the slowdown.
With no sustainable pipeline of projects,
investments into new equipment definitely
slowed and the growing preference for
used equipment became apparent. African
fleet operators particularly are renowned
for preferring this gear.
In a recent conversation with a
representative of a major international
OEM, he noted that the challenge today
is that Africa is a market with the biggest
number of used machines. He reiterated
that when talking of used gear, he wasn’t
even refering to typical five to seven-year
old machines that are the norm elsewhere
in the world. In Africa, you can get a 20-
year old excavator or even a 25-year old
grader still working on site, and it would
have changed hands more than five times
with no form of ownership history at the
disposal of a potential next buyer.
As you will see in the Equipment
Rebuilds feature in this edition of
Capital Equipment News,
it is
encouraging to note that in order
to optimise the lifecycles of their
equipment, both mining and construction
equipment owners are resorting to
refurbished and rebuilt gear. Equipment
users understand the importance
of preserving their investments by
extending their equipment’s life by
having it refurbished or rebuilt. Both
refurbishing and rebuilding improve the
machine’s dependability while increasing
productivity and lowering production and
operating costs.
However, there are very thin, but clear
borders between used (as is), refurbished
and rebuilt equipment, meaning that they
are not one and the same thing. Though the
three terms insinuate previous ownership,
often used equipment is just bought with no
available previous maintenance records or
knowledge of previous concerns, while rebuilt
equipment, when done under OEM standards,
complies with quality standards, often with
the same warranty options as new gear.
Though rebuilt equipment is often
backed by standards, different vendors
use different processes, parts, levels of
exactitude and quality-acceptance levels to
rebuild the equipment they sell.
It is often the norm that when times are
this tough, price is the prime determinant
of what we buy, but when the equipment
you are buying is business-critical, quality
and authenticity should be your most
important considerations. When buying
rebuilt equipment, there is a level of
certainty premised on the fact that a rebuilt
piece of equipment often has a warranty
and possible maintenance programme.
Should it fail, it will be under the same
level of protection as new equipment.
Used equipment may have the price
appeal compared with rebuilt, but I
believe that when buying business-
crucial equipment, it is noteworthy to
look beyond the price tag. Nothing can be
worse than buying a piece of equipment
at a bargain, only to have it fail shortly
after it is deployed at a crucial jobsite
where any form of downtime is out of
question, especially considering that
project timelines of today are unforgiving.
If you make a mistake on a small
appliance, you will have few regrets and
move on. That same mistake on a big piece
of construction or mining equipment has
far reaching implications that will haunt
you for the long haul.
MAKING THE OLD
NEW AGAIN
@CapEquipNewsMunesu Shoko – Editor
capnews@crown.co.za