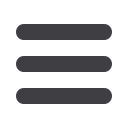

September 2015
Doors, Windows, Floors & Walls
T
he new windscreen recycling
initiative follows a series of ma-
jor sustainability milestones
achieved by Interface since its found-
er and chairman, Ray Anderson, in
1996 put the company on a Mission
Zero journey to become the world’s
first sustainable restorative carpet
producer by 2020. Measures already
introduced by the company include
production driven by biogas derived
from chocolate and fish waste, con-
verting old fishing nets into yarn,
and using castor beans to reduce
the company’s dependency on oil for
carpet production. Interface flooring
has its main production plant in the
Netherlands and is locally distributed
by the Kevin Bates Albert Carpets
(KBAC) group.
Lesley Fidrmuc, Interface Consul-
tant for KBAC, says there are over
a billion cars in the world of which
at least 5 to 6% have windscreens
replaced annually. “The European
Union has been pushing for the
recycling of these windscreens and
now the laminate material, called
Poly Vinyl Butral (PVB), that prevents
the windows from shattering, has
been given a second life. Interface is
collaborating with several European
partners to create a new supply chain
of recycled glass which the company
is now using as replacement for its
existing latex carpet precoat, reduc-
ing the production carbon footprint
by 0.7kg of carbon dioxide per square
metre, equivalent to an 80% reduc-
tion. The precoat is a key component
of carpet as it keeps the yarn stuck
to the backing,” Fidrmuc explained.
Several innovative recycling devel-
opments have led to the availability
of the PVB dispersion now used by
Interface as a replacement for latex
at its plant at Scherpenzeel. “The
windscreens are sent to glass re-
cycling facilities in Belgium and
Germany where the glass is
separated from the PVB and
other materials using a se-
ries of advanced separa-
tion techniques. Next
the PVB is purified
with patented technologies by a Bel-
gian company with which Interface
has partnered over the past seven
years to develop a substitute for latex
in carpet. Finally, another Interface
supplier - withwhich Interface has an
exclusivity agreement - compounds
the PVBdispersion tomake it suitable
as latex substitute. The dry, applied
PVB precoat contains 70% recycled
material.”
Fidrmuc says Interface has access
to up to 200 000 tons of recycled
PVB per year. “The use of PVB in-
stead of latex provides consumers
with an infinitely more sustainable
form of carpet. PVB resin is a non-
toxic, non-corrosive product with
exceptional tensile strength, adhe-
sion and elasticity. It is also impact
resistant. Although there are other
carpet manufacturers that use virgin
PVB for backing purposes, Interface
is the first company in the world to
introduce a carpet with a recycled
PVB precoat.
“Interface has incorporated its
passion for ecological preservation in
all its new carpet tile designs which
KBAC distributes in South Africa.
The latest biophilic designs create
visual and physical connections with
nature, using foliage, the sky, rivers,
the sea, as well as other aspects of
nature as dominant features. Local
response has been exceptionally
positive as architects and designers
are now increasingly striving towards
sustainable, responsible construc-
tion and interiors,” she adds.
Brandon Park, Sales Director of
KBAC, says Interface has since the be-
ginning of 2014 been operating with
100% renewable energy in Europe
(both electricity and gas), using vir-
tually no water in its manufacturing
processes and hasmanaged to attain
zerowaste to landfill. “This is particu-
larly significant as carpets contain a
high oil content in the nylon fibres
and thus become non-biodegradable
landfill components,” he explains.
Park says Interface Europe had
by last year reduced its greenhouse
gas emissions by 90%. “From a base
of zero renewable energy in produc-
tion in 1996, the company now uses
a staggering 95% renewable en-
ergy. Greenhouse gas emissions have
dropped by 90% since 1996. Other
major ‘green’ initiatives introduced
by Interface include the insulation
of hot machine parts, installation
of high efficiency boilers, and lower
temperature materials,” he adds.
■
‘Green’ carpet
In a radical move to increase sustainability in the global carpet
industry, recycled automobile windscreen glass is nowbeing used as
manufacturing rawmaterial by Interface, the world’s largest modular
flooring producer.