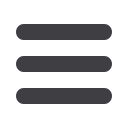

Wire & Cable ASIA – September/October 2007
89
Wir & Cable ASIA – March/April
11
1 State of the art
The diagram below illustrates what
is currently described as the state of
the art process sequence.
1.1 Explanations regarding the
state of the art
Initially the parts are pickled, rinsed
and activated. An alternative to
pickling is mechanical descaling.
This is followed by a zinc phosphate
conversion coating, which is obtained
by means of a chemical reaction.
For many manufacturing processes
a conversion coating is essential to
achieve high quality, cost effective
large-scale production.
The parts being processed are again
rinsed, neutralised and finally a
lubricant is applied.
The lubricants are water-soluble
soaps that react with the conversion
coat or, alternatively molybdenum
disulphide (MoS
2
) dispersions. The
complete process sequence takes
between 60 and 90 minutes.
It is worth noting that the quality of
the phosphate, and the subsequent
performance results, are a reflection
on how much care has been taken in
the early process stages.
2 Zinc phosphates
Currently there are three types of
zinc phosphate commonly in use.
These are defined by their means of
acceleration.
They are:
Nitrite/nitrate
•
Chlorate/nitrate
•
Nitrate/air (Fe side process)
•
Nitrite/nitrate is the most widely used
outside Central Europe. The system
operates at high temperatures pro-
ducing sludge that settles at the bottom of the process
tank. The most common form of accelerator is sodium
nitrite. These processes commonly contain nickel, which
acts as a refining agent.
Chlorate/nitrate processes are used for specific situations
where either the operation is more suited to this method
of acceleration, such as intermittent working, or the
phosphate produced meets a particular demand.
Sludge is also produced in the process tank by this system.
Nitrate/air (Fe side processes) operate at lower temperatures
and produce their sludge in an external tank into which a
controlled supply of air is introduced.
The sludge produced is hard and dense, and settles readily
at the bottom of the tank. These processes are nickel and
nitrite free.
3 Activation
To obtain the maximum benefits from a zinc phosphate
coating the use of an activator prior to the zinc phosphate
is highly recommended.
The activator provides sites for the nucleation of the zinc
phosphate crystals, which produces a refined, controlled,
crystalline coating.
Comparison of the coating thickness of various lubricants
Lubricant layer g/m
2
Polymer
MoS
2
Soap
Figure 2
❍
❍
: Comparison of the coating thickness of various lubricants
Cross-section of a treatment plant
Return flow
Feed calcium
phosphate
Grid anodes
Phosphating solution
Cathode
Wire and solid part
Figure 3
❍
❍
: Cross-section of a treatment plant