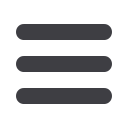

EuroWire – May 2012
34
News
Technology
The
rod
Dry
Cleaning,
Coating
and
Drawing
(DCCD)
process
revolutionises
wire
drawing
by
replacing
conventional
rod
wet
preparation including acid cleaning/
rinsing/wet pre-coating chemicals and
drying by a new totally dry process
that offers substantial cost savings and
a unique combination of simplicity and
effectiveness.
The DCCD process is used in the most
demanding H/C and L/C drawing
applications
from
mechanically
descaled uncoated rod, including 0.90%C,
drawn directly without wet pre-coating
chemicals, including spring wire, PC
strand wire, plating wire, CO
2
welding
wire, etc. The process operates at ‘zero’
maintenance cost as there are no acids,
no hot liquid tanks for rod pre-coating,
no hot air blowers to dry wet rod, and
it operates at virtually ‘zero’ energy
consumption.
An added benefit is the automatic
control
of
lubrication
parameters,
including
lubricant
pressure,
temperature and viscosity, enabling
the use of anti-friction standard high
melting lubricants (200-240°C / 392-464°F
for H/C wire) which are instantaneously
converted from solid into a liquefied state
and deposited on mechanically descaled
uncoated rod, generating exceptional
thermal stability at the highest drawing
speed, 18m/sec (3,600 ft/min) for spring
wire, completely eliminating the need
for phosphate and borax pre-coating
chemicals and their wet substitutes.
In operation, all lubrication parameters
‘communicate’ together in a sensitive
and automatic multi-way interaction to
form a high-density full-film anti-wear
lubricant
coat,
weight-adjustable,
enabling frictionless drawing by physical
separation of wire-die contact in all drafts,
at extreme speed dictated mainly by rod
pay-off and wire take up modes.
Decalub – France
Website
:
www.decalub.comRod preparation: Dry
vs wet. Anti-friction
high melting lubricants
eliminate wet pre-coating
Advertorial on behalf of Decalub
▲
▲
Rod dry coating by LVC/PDH system, in a 0.85%C
application
WTM’s range of concentric taping lines,
with horizontal or vertical lay-out, is
able to satisfy any request for the tape
application in the production of special
wires and cables, even providing in-line
thermal treatment by heating and
sintering ovens.
Thanks to the extreme accuracy of its
technology, WTM proposes taping lines
working with rotation speeds up to
3,000rpm, maintaining the precision of
a few hundredths of a millimetre in the
tape deposition.
The machines can be equipped with fully
electronic taping heads with multiple
motors, suitable to control the tape
tension from 30 Newton down to 100
grams. A special electronic system allows
direct control of the tape tension in each
working condition, even with the most
critical taping materials.
Spinning heads for yarns are also available
with the same precision and capability.
A vision system, with a feedback signal
provided by a camera, can be installed in
all cases where a continuous monitoring
and adjustment of the tape position is
required during the taping process.
WTM Srl – Italy
Website
:
www.wtmachinery.comOne step ahead in cable taping