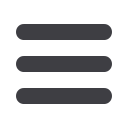

10
M
ay
2011
www.read-tpt.com›
I
ndustry
N
ews
RESPONDING to the need for more test
channels to detect smaller and smaller
defects without sacrificing speed, Magnetic
Analysis Corp engineers developed a new
multiplexed ultrasonic transducer design
for the way transducers send and receive
signals. MAC’s new multiplex 180mm
Echomac
®
ultrasonic rotary system was
recently installed in a Russian plant that
produces oil country tubular goods.
The unit is part of a test station that
inspects welded ERW line pipe and casing
tube up to 168mm diameter and 7.5mm
wall thickness for lamination, wall thickness,
and transverse/longitudinal defects. Using
the new, fully multiplexed 32 transducer
elements that feed 20 channels, results were
excellent even when testing to 5% threshold,
meeting API standards.
MAC’s ultrasonic unit is mounted on a
triple drive roll bench installed as part of
the customer’s in-line test system. MAC’s
bench provides constant centring, which
reduces vibrations and allows for leading
and trailing upset ends to be accommodated.
The entire plant’s production passes the
test station, which has integrated the MAC
ultrasonic system with an existing magnetic
flux leakage test unit. MAC’s bench was
synchronised with the customer’s conveyor
test speed, height, and logic controls. A
new multi-collector computer receives data
from all testing stations and presents a
single traceable report for each tube. The
multiplex feature will also be extended to
other ultrasonic rotaries in MAC’s product
line. MAC also offers flux leakage and eddy
current systems for testing tube, bar, wire
and parts.
Magnetic Analysis Corp
– USA
Email:
info@mac-ndt.comWebsite:
www.mac-ndt.comFirst UT rotary system successfully installed
Baoji
Petroleum
chooses
Thermatool
BAOJI Petroleum Steel Pipe, a division
of China National Petroleum Corporation
(CNPC), an API producer located in the
Shaanxi Provence of China, is currently
installing the world’s largest Thermatool
HAZControl Technology™ (HCT) high
frequency welder. Thermatool has
developed new technology specifically for
this HF Welder, building an 800kW welder
with stabilised frequency adjustment
in 1kHz increments between 275 and
375kHz.
This welder is the first in its class
on multiple fronts. It is the world’s first
true variable frequency welder with
output of 800kW, providing precision HF
welding control to the API market. It
operates at the highest frequency (up to
375kHz) for a solid state HF welder at
800kW. Thermatool has found that higher
frequencies are necessary for welding
some of the most demanding materials
like P110, N80, and stainless and duplex
steels. It is the first high-powered welder to
be controlled with Thermatool’s patented
HAZControl Technology™.
More and more customers are
selecting HCT as their welder of choice.
The new welder is the first to be capable
of achieving full power output over the
frequency range (275–375kHz) in either
induction or contact welding mode.
Dual welders add flexibility for producers
who need to minimise kilowatt hours/ton
cost in their HF welding equipment. It is
the first high-powered HCT welder fitted
with Thermatool’s new contact welding
system using the QuadContact™ design.
Four contact tips reduce marking on
pipe during HF welding and increase the
life of the contacts, once again adding
differentiation to Baoji’s product offering.
Control of the Heat Affected Zone (HAZ)
is essential for ensuring repeatability of
HF welder performance. As new high
performance steel alloys are introduced
into the OCTG pipe and tube (API) market,
the process windows for achieving the
best weld are tightened. HAZControl
Technology™ provides a means by which
these new materials can be welded with
consistency.
The tube producer benefits with
stronger materials and stronger welds,
produced with less scrap. This new welder
allows Baoji to produce product up to
219.1mm OD with 13.72mm wall while
maintaining tight control over the HAZ.
With its 800kW Thermatool VF Welder,
Baoji is breaking new ground and helping
bring oil and gas tubular product to a new,
higher standard.
Hypertherm designs and manufactures
the world’s most advanced plasma cutting
systems for use in a variety of industries
such as shipbuilding, manufacturing and
automotive repair.
Its product line includes handheld
and mechanised plasma cutters and
consumables, as well as CNC motion and
height controls. Hypertherm systems are
trusted for fast, precision metal cutting
and reliability that results in increased
productivity and profitability for tens of
thousands of businesses.
Hypertherm
– USA
Website:
www.hypertherm.comThe new multiplexed
ultrasonic transducer design