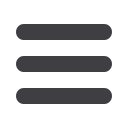

29
11.0 ESTABLISHING SUPPORTING ACTIVITIES
Prior to and during the case study, there was
already in place a large internal company
network of safety practitioners with different
safety objectives and operational safety
standards.
Other internal businesses had developed future
plans for certification.
Consequently it was essential to establish, at an
early stage in the process, a common repository
for information exchange.
This was achieved in the form of a Safety
Database containing the following information:
• Third-party certificates of safety products
• Lists of certified functional safety engineers
and functional safety technology engineers
• Improvement themes
• Technical papers and articles
• Latest FSMS procedures
• External functional safety standards
• Sales and technical product material
• Case study progress and program updates
12.0 MANAGING CHANNEL PARTNERS AND
THIRD-PARTY INTEGRATORS
The same rigorous approach to functional
safety had to apply to any third-party integrators
being used by any of the company’s integrators.
This ensured the safety and quality of the third-
party integrator. A program of work was
required to perform a gap assessment on third-
party integrators and to subsequently work with
them to ensure that they developed a compliant
functional safety management system,
preferably in line with that of the main system
vendor. This process has been seen to benefit
the third-parties in that they can also achieve
certification and capitalize on the achievement
in the safety market place.