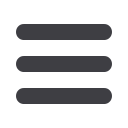

J
uly
2008
www.read-tpt.com22
›
T
echnology
U
pdate
on the welded component. In contrast to
conventional TIG welding, non-contact
laser welding achieves higher process
speeds, and the weld seams generated are
capable of withstanding high stress levels
without tearing.
The Profile Welding System consists of
a beam guidance and sensor system
together with PC-controlled linear axes.
All laser system functions, such as control
of process gases, monitoring of the optical
safety circuit and overall monitoring of the
laser system and its associated cooling
system, are handled by the integrated PLC
control system.
Rofin’s Profile Welding System
The sensors used for weld seam position
recognition and seam tracking can detect
the slightest discrepancies in the seam
position. This adaptive system ensures
that the laser beam always follows the
seam, providing high process reliability
and consistency. The high-speed precision
linear drives used by the Profile Welding
System provide positional accuracies
of 20µm at production speeds of up to
60m/min.
A field proven beam delivery system on
the Profile Welding System provides safe
operation under tough industrial conditions.
The system is not sensitive to oil, dirt, dust
or damp and is also virtually maintenance
free, providing high uptimes and reliability.
A display unit mounted on a moveable
support arm provides ease of use
for operators. This allows centralised
monitoring and optimisation of the laser
parameters and functions together with
seam tracking on the workpiece.
Designed with modular construction in
mind, the system can be easily configured
to suit specific requirements. For example,
the beam guidance system can be
supplied with either a beam switch unit or
a beam splitter unit, the latter enabling
simultaneous operation on several systems
or alternatively at multiple welding points.
A number of options are also available for
the Profile Welding System that can be
used to further customise its configuration
for a specific application. These include
process gas jet geometries configured for
the application; a 30° rotating weld head,
enabling ‘drag welding’ for higher welding
speeds; and process data monitoring and
storage for quality purposes.
The Profile Welding System is based upon
the successful range of Rofin CO
2
slab
lasers. With up to 8kW of output power
available and excellent beam quality
Multi-station production of complex parts
Trans-Bar machines from Buffoli Transfer SpA, Italy, are multi-spindle CNC transfer
machines fed with non-rotating bars or tubes of any profile and material.
A bundle type tube feeder, integrated with
the machine, automatically loads tubes up to
6m in length, and up to 75mm in diameter.
In the first station, the tube is cut-off and
the consequent slug/blank is then indexed
from station to station in order to machine
the entire external and internal diameter,
and also any radial operations, allowing the
production of complex parts.
During machining the parts may be clamped
with jaws, collets or high precision self-
centring chucks that are positioned on the
perimeter of an indexing turret of between
4 and 20 stations. The part is completely
machined internally and externally with
numerous tools working simultaneously
from more than one direction (opposing,
transversal and inclined). At any station
the semi-machined parts can be rotated,
allowing machining of high precision parts
as well as very long parts.
The machines are suitable for the complete
machining of turned parts without costly secondary operations. While the machines
are quickly re-tooled, like a two-spindle CNC lathe, they offer higher productivity than
a multi-spindle screw machine. Thay also allow the complete processing of parts that
cannot be completely machined on lathes.
Average setup times range from 30 to 90 minutes, and a wide range of quick-
change accessories are available, allowing production batches of a few thousand
parts. Machines with tube sizes up to 45mm are also produced in double production
versions, and can reach four times the productivity of a multi-spindle lathe (up to
12,000 parts/hr).
Buffoli Transfer SpA
– Italy
Fax
: +39 030 201556 •
:
info@buffoli.it•
Website
:
www.buffoli.itThe Macro Group of Rofin, Germany, has
launched a new Profile Welding System
designed and configured to weld tubes
and profiles using fully integrated sensor
technology. This technology is designed
to detect the weld gap and enable seam
tracking.
The laser welding process for joining tube
and profiles enables narrow seams with
fine grain structure to be produced together
with a minimum of heat affected zone.
The controlled and predictable nature of
the laser welding process also means
that in the majority of cases, no further
heat treatment or processing is required
Buffoli machines can be used to machine
turned parts without costly secondary
operations
Profile welding system with
fully integrated sensor technology