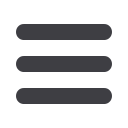

J
uly
2008
www.read-tpt.com30
T
echnology
U
pdate
›
Brushes for pipeline weld cleaning
Osborn International, Germany, manu-
factures brushes and abrasives for use
in the industrial, trade and private sector.
Steel wire brushes are an ideal solution
for the cleaning of welded seams.
Wire brushes are a cost effective and
practical method for removing welding
cinder and beads that prevent the next
seam from being applied. The use of
cellulose and alkaline electrodes are
insignificant, as the brush will carefully
remove all types of cinder.
A rotating wire brush will provide a clean
welded seam without having to remove
up to 30 per cent of the welding material,
as is inevitable with a grinding disc. Any
defects in the weld seam also become
immediately visible, enabling any rework
to be carried out promptly.
The use of steel wire brushes reduces
the number of seams by a claimed 30-50
per cent, and additional time needed for
resoldering work can be avoided. Osborn
pipeline brushes can be used for weld
cleaning, internal or external cleaning,
bevel end cleaning, removal of insulation
coats and rehabilitation work. They enable
long life, optimal brushing results and safe
work.
Osborn International GmbH
– Germany
Fax
: +49 64 5158 8206 •
Website
:
www.pipelinebrush.com
Cleaning a welded seam using a rotating wire
brush
A pipeline brush from Osborn
Weldlogic Europe, UK, has developed the
Black Diamond welding chamber which
features a large work space with stainless
steel work surface. The chamber has a
large transfer load-lock with automatic
timed gas purge, while gas welding quality
is assured by an oxygen meter display in
parts per million.
The workstation is ready to operate, only
requiring the fitting of the user’s weld
system and connection to gas and power.
It can be installed on bench top for standing
or low seated operation. Other features
include attainable gas purity below 5ppm
oxygen for bright nickel weld finish, and
fully automatic load-lock gas management
control system.
The Black Diamond welding chamber
provides a system design that is a cost-
Ultimate welding chamber ideal
for TIG welding materials
effective solution to TIG welding materials
reactive to atmospheric contamination. It
can also be used for high-end materials
that require a controlled and verified
welding environment for minimal defect and
tarnished work pieces.
The bench top mounted workstation has
two 6" x 8" oval polypropylene glove
ports mounted below a 10mm thick
polycarbonate window. The weld chamber
is manufactured in virtually indestructible
textured copolymer, and is fully welded and
leak tested.
The chamber is fitted with a stainless steel
floor plate over box length of 950mm and
depth of 550mm within a height of 650mm.
A rear panel is removable for occasional
cleaning or installing large welding aids.
Weld cable connectors are ready for hook
up to torch, ground and power source,
including gas feedthrough fitting for torch
shield gas.
The load-lock is constructed in the same
copolymer, and is fully welded and leak
tested. Inner and outer doors of the same
material are reinforced for ensuring effective
sealing with captive ‘O’ ring seal. The doors
operate using lever latch clamping. The
rectangular design provides a 380mm length
load-lock with 280mm depth and 280mm
height for easy transfer of most large
weld pieces. A stainless steel floor plate is
supplied for ease of weld piece transfers.
A push button initiates a gas purge to
remove air and replace it with argon gas
for transfer of weld pieces into the weld
chamber without degrading the main
chamber argon gas purity. Set time and
gas flow ensures quality controlled transfer
with minimum gas usage, and an audible
sounder announces completion of the gas
purge process.
The glove box workstation is equipped
with a twin fluorescent light, externally top
mounted over a polycarbonate window to
provide over 700 lux of lighting within the
glove box at the working plane.
The weld chamber is supplied with a gas
flow regulating valve and flow gauge to
adjust the amount of argon passing through.
This regulation allows for the chamber to be
set at a flow rate to reduce and hold the
oxygen levels to below 5 parts per million.
Argon gas consumption varies according to
use but averages below 10 litres per minute
during operation and 1 to 2 litres per minute
on standby. Initial gas purge of the weld
chamber – from air down to weld quality is
less than 60 minutes at less than 50 litres
per minute gas flow.
Weldlogic Europe Ltd
– UK
Fax
: +44 1480 437479
:
weld@weldlogic.co.ukWebsite
:
www.weldlogic.co.uk
The Black Diamond welding chamber from
Weldlogic