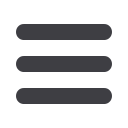

J
uly
2008
www.read-tpt.com38
T
echnology
U
pdate
›
Eagle Precision Technologies Limited,
Canada, has designed, manufactured
and delivered a unique machine for the
automated assembly of heat exchangers.
As a result of a customer request, Eagle
was challenged to design and manufacture
a machine for the assembly of heat
exchangers in a more effective process,
to offset the higher cost of the technology
used to meet new efficiency standards.
The main component of home heating
furnaces, both forced air and hot water,
is the heat exchanger. This component
takes the heat produced by burning fuel
and transfers it to the water or air for
distribution throughout the house. The HX
(heat exchanger) tubes must be assembled
to the HX panel ensuring an airtight lock
so that internal combustible gas does not
escape into the ventilation chamber of the
furnace. This lock must also be verified to
a predetermined ‘leak rate’ that adheres to
industry standards.
The most common method for fastening
the two components is the ‘ridge lock’.
This process involves introducing a set of
segmented expand tooling into the tube and
expanding a bead around both sides of the
panel flange. The result is an interference
lock between the HX tube and the HX
panel. Eagle has supplied this proven
technology to the industry for over 20 years.
The problem has always been the slower
cycle times required to complete larger,
multiple tube panels. Also, inspection of
the completed assembly required a second
operation.
Eagle’s new line of fully automated heat
exchanger assembly machines for the
HVAC industry offers the latest in automation
technology. With this new platform, the
HX panel is scanned and loaded into the
assembly station. The correct part program
is automatically selected and with the touch
of a button, the sequence is initiated.
When the next configuration is scanned,
the new parameter is automatically set,
allowing for zero changeover time. After the
components are locked in place, the entire
assembly is leak tested before being ejected
for transport to the final furnace assembly
station. This new turnkey solution offers
users decreased floor-to-floor cycle times,
fully programmable indexing for multiple
part configurations and fully integrated leak
test capabilities for assured real time quality
assurance of components. Eagle’s HVAC
assembly solution includes heat exchanger
lines capable of assembling 80-90+ per cent
dual stage efficiency furnace components.
According to customer estimates, the new
automated solution is 48 per cent faster
than the previous manufacturing process,
providing significant production savings.
Eagle Precision Technologies Ltd
–
Canada
Fax
: +1 519 756 0195
:
sales@eaglept.comWebsite
:
www.eaglept.comA growing range of
ERW tube and pipe
Conros Group, India, is the manufacturer
of black and galvanised ERW steel tube,
pipe and hollow sections from ½" to 4".
A diversified company with facilities in
Khopoli, India, Conros undertakes activities
including steel manufacturing and trading.
The group has expanded its capacities by
introducing new state-of-the-art equipment,
imported from USA and Europe. The
equipment will be used to manufacture
larger diameter pipes and API line pipes
from 2½" to 8" diameter, and square and
rectangular hollow structural sections.
Conros manufactures tubular pipes in ½"
to 4" diameter, and square and rectangular
sections from 15x15mm to 100x100mm.
The products are produced according to
international and Indian standards including
IS, ASTM, DIN, BS, EN, JIS and ISO.
The company’s upcoming developments
include API 5L accreditation (for 3" to 8"
up to grade X70) by December 2008, and
UL listing (ie UL 6, UL 797 and UL 1242
for conduits) also by December 2008. FM
approval (for fire fighting systems) and CE
marking approval (for European markets)
are both under proposal.
Conros Group
– India
Fax
: +91 22 2660 5454
:
info@conros-group.comWebsite
:
www.conros-group.comNew tube straightening and cutting machine
Ravni Technologies, France, has launched a new tube straightening and cutting
machine. The machine is designed to achieve a very good straightness of around
0.1mm per metre. By using a rotary straightener equipped with preset dies, setting is
easily carried out, and the straightness
quality does not change along the coil.
The cutting operation (fixed or flying
device) is operated by a slitting saw or
a wheel according to specific require-
ments. The machine can straighten
stainless steel, copper, aluminium or
coated tube, from 40 to 80 metres/min.
Ravni Technologies
– France
Fax
: +33 477 90 58 65
:
info@ravni.comWebsite
:
www.ravni.com
The new straightening and cutting machine from
Ravni Technologies
Delivery of automated heat exchanger
manufacturing solution
A typical heat exchanger assembly
The new Eagle 80+ HVAC assembly machine