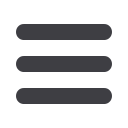

J
uly
2008
www.read-tpt.com88
›
H
eat &
S
urface
T
reatments
of up to 370 x 220 x 200mm (L x W x H).
The maximum weight of parts or batches
is 30kg. This allows the new inline cleaning
system to reach throughput of 2.7 tons per
hour. With dimensions of 7500 x 3500 x
3100mm, it more than meets the demand
for space-saving cleaning technology.
The EcoCSpeed’s flexible design makes it
possible to equip the system with additional
process modules to ensure that the overall
40-second cycle time is maintained. The
work chambers are loaded in a delayed
process by a handling system which is
tailored to the workpiece or the batch.
In the work chambers, the parts are treated
by injection flood washing (IFW), steam
scouring and vacuum drying. For IFW, jet
systems pump the cleaning agent at high
pressure into a flooded work chamber,
producing a whirlpool effect.
Due to the vacuum drying process,
workpieces leave the system completely
dry and ready for immediate downstream
processing.
Dürr Ecoclean GmbH
– Germany
Fax
: +49 711 7006 148
Website
:
www.durr-ecoclean.comand vacuum drying, and the cycle time
can be adjusted to suit the manufacturing
cycle. Cleanliness is achieved even for
stringent specifications. Process quality and
efficiency is ensured by cleaning complex
parts individually rather than in batches.
In the past, short cycle times and strict
cleanliness
requirements
presented
problems for inline cleaning processes,
especially when cleaning complex, mass-
produced workpieces. Very complex,
continuous systems were required, and the
spraying methods used in these systems
were only partially able to clean the parts.
The innovative EcoCSpeed system, which is
equipped with several process modules, was
designed to be integrated into production
lines, or directly connected to production
systems and machining centres. The
workpieces can be cleaned individually or as
a batch from production in a product carrier.
The basic version of the EcoCSpeed is
equipped with five process modules, which
are designed for part/batch dimensions
Dürr Ecoclean GmbH, Germany, has
introduced the EcoCSpeed for inline
cleaning of individual parts. This innovative
system makes it possible to clean complex
geometrical
workpieces
during
the
manufacturing cycle using non-halogenated
hydrocarbon.
The EcoCSpeed has several process
modules that can be loaded in delayed
phases via a specially designed handling
system. The cleaning process may include
injection flood washing, steam scouring,
Hydrocarbon system for inline, individual
part cleaning in cycles
The EcoCSpeed is used for inline cleaning of
individual parts
n