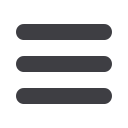

643
www.grovegear.com
High Efficiency Helical - Bevel
Gear Reducers
High Efficiency Parallel Shaft
Gear Reducers
Stainless Steel
&
WASHGUARD
®
High Efficiency Gear Reducers
Technical Information
Warnings and Cautions
Terms and Conditions
It is the responsibility of the original equipment manufacturer or user to install
and/or operate Ohio Gear Products in conformance with applicable local and
national safety codes, suitable guards for rotating shafts and couplings should
be used at all times. Good safety procedures should always be observed
whenever working with or around any transmission equipment. Fitness for
XVH LV WKH FXVWRPHU·V GHFLVLRQ DQG UHVSRQVLELOLW\
SERVICE FACTORS
– Numbers whichmodify the loads whichmust be considered in
selecting a speed reducer are called service factors. They vary with the type of service
in which the reducer is to be used, the kind of prime mover involved and the duty cycle.
WORM GEAR REDUCER SERVICE FACTORS
3URSHU GHWHUPLQDWLRQ RI DQ DSSOLFDWLRQ·V VHUYLFH IDFWRU FKDUDFWHULVWLFV LV FULWLFDO IRU
maximum reducer life and trouble free service. See the definition of service factor in
the glossary.
All Grove Gear reducers and Gear+Motors™ are sized for applications having an
AGMA defined service of 1.0, unless otherwise stated. (Alternately, 1.0 service
factor is sometimes expressed as “Class I Service”.) Reducers in such applications
operate on a continuous duty basis, for 10 hours per day or less, and are free of
recurrent shock loads. When operating characteristics are different than noted, the
input horsepower and torque ratings listed must be divided by the service factor
selected from the table below. This table applies to reducers with an electric or
hydraulic motor input.
SPECIAL APPLICATION CONSIDERATIONS
: Please contact Grove Gear for assistance in applications not
listed or for applications with unusual characteristics. Including the following:
,QSXW VSHHGV QRW OLVWHG LQ FDWDORJ
)UHTXHQW VWDUWLQJ RU UHSHWLWLYH VKRFN DSSOLFDWLRQV
6HOHFWLRQ RI UHGXFHUV IRU PDQ OLIWV RU SHRSOH PRYLQJ HTXLSPHQW
+LJK HQHUJ\ ORDGV LQFOXGLQJ VWDOOLQJ
WORM REDUCERS:
6WDUWLQJ RU PRPHQWDU\ RYHUORDGV H[FHHGLQJ
RI JHDU UHGXFHU
mechanical capacity (100% overload)
SERVICE FACTOR TABLE
When a single or multi-cylinder engine is the input power, the service factor
selected from the table above should be increased by multiplying the value by the
factor selected from the table below.
Service Factor Conversion Table for Engine Driven Applications.
On page 644, AGMA standardized service factor data is listed for a wide variety
of applications operating 3 to 10 hours per day and for 10 hours or more per day.
BACK-DRIVING
– This is the converse of self-locking. Depending upon ratio and
many variables, it is difficult to predict the back-driving capability of a reducer. Worm
gear reducers are not intended to be used as speed increasers. Consult factory for
back-driving applications.
PEOPLE CONVEYING EQUIPMENT
– Selection of gear drives for applications
whose primary purpose is the transportation of people is not approved. This includes
such applications as freight or passenger elevators, escalators, man lift platforms,
and ski tows and ski lifts.
If the primary purpose of the application is material conveyance and occasionally
people are transported, the warranty may remain in effect provided the design and
load conditions are not exceeded and certification to the appropriate safety codes
and load conditions has been obtained by the system designer or end user from the
appropriate enforcement authorities.
STORED & INACTIVE GEAR DRIVE
– Each drive is protected with rust preventive
that will protect parts against rust for a period of 6 months in an indoor dry shelter.
If a drive is to be stored, or is inactive after installation beyond the above periods,
drain oil from housing and spray all internal parts with a rust preventive oil that
is soluble in lubricating oil and rotate the shafts several times by hand. Before
operating, drives which have been stored or inactive must be filled to the proper level.
Periodically inspect stored or inactive gear drives and spray or add rust inhibitor every
six months, or more often if necessary. Indoor dry storage is recommended.
EXCESSIVE OVERLOADS
– The maximum momentary or starting load must not
exceed 300% of rated load (200% overload). Rated load is defined as gear drive
rating with a service factor of 1.0. If the maximum starting or momentary load
exceeds the above conditions, compute a second equivalent power rating by dividing
the peak load by two. The gear drive selected must have capacity equal to, or in
excess of, the larger equivalent power rating.
REVERSING SERVICE
– Applications involving either more than 20 reversals per
ten hour period, or less than 20 reversals per ten hour period with peak torques
greater than 200% of normal load must be referred to Factory.
BRAKE EQUIPPED APPLICATIONS
– When a gear drive is equipped with a
“working” brake that is used to decelerate the motion of the system and the brake is
located between the prime mover and the gear drive, select the drive based on the
brake rating or highest equivalent power rating, whichever is greater. If the brake is
used for holding only and is applied after the motion of the system has come to rest,
the brake rating must be less than 200% of the catalog rating, refer the application
to Factory. Also refer to Factory all applications in which the brake is located on the
output shaft of the gear drive.
OVERSIZED PRIME MOVER
– Published service factors do not cover applications
that require oversize prime movers for high energy or peak loads. Refer such
applications to Factory for selection of suitable drives.
MAXIMUM INPUT SPEEDS FOR WORM GEAR REDUCERS
(GR, NH, EL SERIES)
Size 813 through 852 2500 RPM
Size 860 through 8100 1750 RPM
NOTE: Horsepower ratings for 1750 RPM should not be exceeded when operating
at higher input speeds. For higher input speeds, contact Factory.
APPLICATION CONSIDERATIONS:
Belt Conveyors – To determine the torque, establish the belt pull. In calculating this,
the effects of sliding friction and angle or inclination must be considered. The table
below shows application factors which may be sued in determining belt pull based
upon common combinations of materials and various angles.
Material Combinations
Angle from the Horizontal
0°
10° 20° 30° 40° 50° 60° 70° 80° 90°
Pivoting Bucket Conveyor 0.025 0.19 0.36 0.52 0.66 0.78 0.88 0.95 0.99 1.00
Belt on Rollers
0.025 0.19 0.36 0.52 0.66 0.78 0.88 0.95 0.99 1.00
Metal on Metal (Finished)
0.20 0.37 0.53 0.67 0.80 0.89 0.97 1.01 1.02 1.00
Fabric on Steel
0.27 0.44 0.60 0.74 0.85 0.94 1.00 1.03 1.03 1.00
Fabric on Wood
0.32 0.49 0.63 0.77 0.88 0.97 1.02 1.04 1.04 1.00
Leather on Wood
0.35 0.52 0.67 0.80 0.91 0.99 1.04 1.06 1.05 1.00
Wood on Wood
0.35 0.52 0.67 0.80 0.91 0.99 1.04 1.06 1.05 1.00
Plastic on Steel
0.35 0.52 0.67 0.80 0.91 0.99 1.04 1.06 1.05 1.00
Metal on Wood
0.40 0.57 0.72 0.85 0.95 1.02 1.07 1.08 1.05 1.00
Rubber on Wood
0.45 0.62 0.76 0.89 0.99 1.05 1.09 1.09 1.06 1.00
Rubber on Steel
0.50 0.67 0.81 0.93 1.03 1.09 1.12 1.11 1.07 1.00
Leather on Metal
0.56 0.72 0.87 0.98 1.06 1.12 1.14 1.13 1.08 1.00
The procedure involves selection of the proper application factor for the calculations:
Belt Pull = (Total Weight on Conveyor) x (Application Factor)
Torque = (Belt Pull) x (Radius of Head Pulley)
Example: An inclined belt conveyor is to move boxes of steel parts. The belt is fabric
on rollers. Five boxes will be on the conveyor at a time, and each weighs 50 pounds.
The conveyor is inclined at 10° to the horizontal, and the head pulley diameter is 7”.
How much torque is required at the head pulley?
Select .44 as the application factor.
Determine weight: 5 x 50 = 250 Lbs.
Determine belt pull: 250 x .44 = 110 Lbs.
Determine torque: 110 x 3.5 = 385 Lb. Ins.
HOISTS
– A worm gear is generally said to be self-locking or irreversible when the
gear cannot drive the worm. This static condition can be upset by vibrations from
nearby machinery or other sources. Many worm gear reducers are not self-locking,
and even a particular size and ratio, which may appear to be, cannot be depended
upon for this purpose. Also, a reducer which holds the load when upward movement
is stopped may not when the load inertia is moving downward and the motor is
stopped. For complete locking assurance, it is recommended that a fail-safe brake
be used for such an application.
CAUTION
Technical Information
Duration of Service
Uniform
Moderate
Heavy
Extreme
(Hours per day)
Load
Shock
Shock
Shock
Occasional 1/2 Hour
—*
—*
1.00
1.25
Less than 3 Hours
1.00
1.00
1.25
1.50
3 - 10 Hours
1.00
1.25
1.50
1.75
Over 10 Hours
1.25
1.50
1.75
2.00
* Unspecified service factors should be 1.00 or as agreed upon by the user and manufacturer.
Hydraulic or Electric
Single Cylinder
Multi-Cylinder
Motor
Engines
Engines
1.00
1.50
1.25
1.25
1.75
1.50
1.50
2.00
1.75
1.75
2.25
2.00
2.00
2.50
2.25
CAUTION