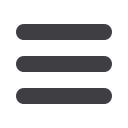

News
Technology
July 2017
35
www.read-eurowire.comUnavoidable fines (abrasive
particles) generation, the
most destructive lubricant
contaminants
in
wire
drawing, is no longer an
alarming
phenomenon
since the introduction of
the Decalub green and dry
rod preparation and wire
lubrication including PDH
coating system.
In the most demanding
wire drawing applications, the PDH die’s
wear is reduced to a unmeasurable level
(about 0.2 micron per tonne), meaning
that three-body abrasive wear is virtually
eliminated, thus revolutionising the wire
drawing process.
The PDH lubricant film created is of such a
configuration as to induce a hydrodynamic
lubricant activity causing migration of all
lubricant contaminants, including fines,
rust oxide and scale, without interference
with the die, meaning the removal of
encapsulated
abrasive
particles prevents die wear,
enabling wire frictionless
drawing at extreme speed
and much lower temperature,
and achieving an excellent
wire smooth finish not
difficult to water clean in-line.
Applications include all plain
carbon wires up to 0.98
per cent carbon, coated or
uncoated, and stainless steel
alloy wires up to 26 per cent chromium,
where the PDH high-performance specific
anti-friction coat is automatically controlled
in hardness and thickness, adjustable at
will up to 15 microns, largely sufficient to
capture, encapsulate and retain liberated
abrasive particles from wire surface and
ensure abrasive particles removal without
interference with drawing dies.
Decalub – France
:
info@decalub.comWebsite
:
www.decalub.comMELOS
and
cooperation
partner
Inhol offer a wide range of radiation
cross-linkable, high temperature-resistant
compounds for automotive applications
such as battery cables and primary wire.
Various halogen-free and halogenated
products are formulated to meet
standards like SAE, HMC, JASO, ISO
and LV. Automotive wires, made of
Melos Cable Compounds, have been
approved worldwide by well-known car
manufacturers. The Mecoline RDX product
portfolio features a variety of solutions for
cable and wire manufacturers supplying
to the automotive industry.
The Mecoline range consists of six
thin-wall insulation compounds for
primary wire, selected to meet the high
demands of the industry. Furthermore,
several solutions for battery cables can
be chosen, including full- or semi-flexible
and oil-resistant compounds, based on
either polyolefins or fluoroelastomers.
Halogen-free
insulation
compounds
(Mecoline I RDX 1213 F & Mecoline I
RDX 1229 F) are suitable for operating
temperatures up to 125°C.
These fast-curing radiation cross-linkable
formulations can be processed at very
high line speeds. The main applications
include small gauge primary insulation
(SAE J1128) and appliance wire.
To reach the higher spheres of the
thermometer,
you
should
consider
halogenated Mecoline RDX compounds.
Maximum operating temperatures of 150°C
to 225°C can be achieved. For temperatures
over
200°C,
sophisticated
form-
ulations based on fluoropolymers are
required.
Additionally, certain products offer
high abrasion- or chemical media-
resistance, flexibility and unique setups
to serve applications such as battery
cables in hybrid cars or electric vehicles.
Formulations are specifically designed for
standards like ISO 6722, ISO 14572, SAE
J1127 or SAE J1128.
Melos GmbH – Germany
Website
:
www.melos-gmbh.comInhol BV – The Netherlands
Website
:
www.inhol.comCompounds for the automotive world
▲
▲
A wide range of radiation cross-linkable, high temperature-resistant compounds for automotive applications
fromMelos and Inhol
Advertorial on behalf of Decalub
Die wear – way to eliminate it
▲
▲
Wire coating by PDH system