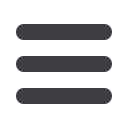

I NSPE C T I ON , T E S T I NG & QUA L I T Y CONT R OL
www.read-tpt.comMARCH 2017
77
Tubular inspection services and equipment
TUBOSCOPE, a division of National
Oilwell Varco, LP (NOV), is a supplier
of tubular inspection services and
equipment to the petroleum and pipe
manufacturing industry. Its technologies
are used for inspecting new and used
tubular goods to demanding industry
and customer specifications, and include
Amalog
®
and Sonoscope
®
electro-
magnetic inspection (EMI) technologies,
and Truscope
®
, TruWall
®
and TruScan
®
ultrasonic (UT) inspection systems.
An example of the capability within
the Tuboscope product line is the
Truscope A/S (Amalog-Sonoscope).
This inspection system combines the
non-destructive techniques of EMI and
UT principles to detect, evaluate and
classify, in a single pass of the pipe
through the system, transverse and
longitudinal, internal and external flaws
as well as wall thickness variations and
laminations.
The Truscope A/S system provides
full-body inspection across a large
range of pipe diameters. The pipes can
be seamless or ERW; manufactured of
ferrous or non-ferrous alloy materials;
and with a variety of end conditions –
saw-cut or cropped, plain-end, threaded,
coupled, and upset or non-upset.
With its combination of EMI (Amalog
and Sonoscope) and UT (Truscope)
techniques, the Truscope A/S satisfies
the latest editions of API 5CT, 5L and 5D,
as well as numerous other international
specifications
for
non-destructive
inspection of tubular products for the
energy industry.
The inspection system comprises two
main sections – the inspection platform
and the computerised inspection
electronics. Placed within a pipe
conveyor line, the pipes are advanced
to the inspection platform. Mounted on
this platform are pinch rolls that contain
the pipe and provide the driving power
to move it at a constant speed though
the three individual inspection heads, or
positioners. The testing sequence is the
Sonoscope first, followed by the Amalog
and ending with the Truscope. All three
positioners are mounted on track roller
systems to allow them to be moved in
or out of the conveyor line for pipe size
change-over or maintenance.
Pipe to be inspected is first conveyed
through the Sonoscope inspection
unit, where a high-strength active
magnetic field orientated longitudinally
is introduced into the pipe. Multiple
stationary detector assemblies, or
‘shoes’, are brought into contact with the
outside diameter pipe surface. Flaws
such as transversely orientated cracks,
rolled-in slugs and pits are detected by
this inspection method.
The pipe is next conveyed through
the Amalog inspection unit, which is
equipped with a dual-shoe detection
system integrated into a rotating mag-
netiser assembly. As the pipe enters the
Amalog inspection unit, a high-strength
active magnetic flux field, circumferen-
tially orientated, is introduced into the
pipe. The rotating detector shoes then
scan the outside surface area of the pipe
circumferentially in a helical path. Flaws
such as longitudinally orientated seams,
cracks and overlaps are detected by this
inspection method.
Tuboscope
– USA
Website:
www.nov.comsema
systemtechnik GmbH & Co. KG
Bredenhop 27
32609 Hüllhorst /GERMANY
Telefon +49 5744/9318-0
www.sema-systemtechnik.de info@sema-systemtechnik.destraightening
for diameters from 5 to 220 mm
For each process the right system
•
Automating
e.g. separating and handling systems
•
Straightening
e.g. 2-, 6- and 10-roll-straightening machines
•
Inspecting
e.g. complete NDT inspection lines and
straightness measuring
•
Sawing
e.g. multi head cut systems
•
End Finishing
e.g. deburring, thread cutting, punching
•
Packaging
e.g. bundling and packaging into
round, square and hexagon bundles
straightening machines
for precise straightening of round tubes