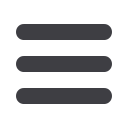

62
Tube Products International January 2010
www.read-tpi.comThe PURE concept consists of a single work step in which the
pipe end is thickened and exactly rounded at the same time.
This is achieved by upsetting the inductively heated pipe ends
against a mandrel and outside mould in a controlled process.
The inside and outside of the pipe end are then machined.
This narrows the tolerance of the inside and outside diameter
to an extent that would be unthinkable in conventionally rolled
pipes. In comparison to rolled pipes of the same dimensions,
the diameter tolerance is just ±0.25mm instead of the usual
±1.6mm. Ovality is no longer a concern. Each pipe can
therefore be immediately welded to the following pipe with
optimal processing parameters and without prior sorting. The
result is a significantly longer service life of the weld under
conditions of dynamic stress.
The key to the design is a curved outer groove, which ensures
optimal stress distribution in relation to the fatigue strength.
The calculations of the engineering team headed by Dipl-Ing
Marion Erdelen-Peppler of Salzgitter Mannesmann Forschung
GmbH in Duisburg played an important role in this project.
After completion of the development, Shell purchased a
total of 650 PURE pipes and subjected them to its own
comprehensive tests.
The results were satisfactory and in November/December
2007 two PURE riser strings were produced onshore for the
URSA platform and reeled onto the giant drums of the pipe-
laying vessel
Technip Deep Blue
.
V&M Deutschland GmbH
– Germany
www.vmtubes.deThe use of different production
batches makes everything even more
complicated. As they usually exhibit
different mechanical properties, the
production batch may also have to be
taken into consideration during sorting
in order to ensure perfect welds. The
result is a puzzle of such complexity
that a solution is not always possible.
The other apparently obvious solution
– using thicker pipe material and
ensuring the necessary equality of the
pipe ends by mechanical machining
– entails considerable disadvantages.
Besides the cost aspect, there is a
weight problem to consider, as the riser
would be much heavier. The platform
would have to be made larger, at not
inconsiderable additional cost, in order
to carry the added weight.
A more serious consideration is that the
crucial wall thickness of the pipe string
would then be at its lowest in the weld zone. In view of the
greater rigidity of the central zone of the pipe, stresses and
deformations – especially during bending – are concentrated
in the weld zones. The consequence is a disproportional
reduction in their dynamic strength.
V&M Tubes has worked on technologies for the fit-for-purpose
preparation of pipe ends for many years. The range of
options includes calibration, internal and external mechanical
machining, and thickening by upsetting.
Volker Rohden commented, “
Shell wanted to utilise this
know-how and therefore in the context of the URSA project, it
requested suggestions for a riser end design that would meet
the end dimension tolerance for SCR welding without any
further machining or sorting of pipes.
”
Finished riser strings on their way to
the drums of the pipe-laying vessel
Welding the pipe string onshore