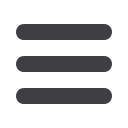

July 2016
Infrastructure and Mixed Use
T
echnical and Product Manager
Renier Snyman explains that
this represents the latest ad-
dition to the 630 mm diameter range
from DPI Plastics.
The company introduced mPVC
piping systems in the 1990s and DPI
Plastrics remains an innovator and
international leader in this market
segment, having supplied technology
licences as far afield as Australia, Asia
and South America.
DPI Plastics manufactures mPVC
pipe in pressure classes from six to
25 bar, and in standard 6 m lengths,
complete with spigot, integral socket
and rubber ring seal for ease of instal-
lation. All the products are manufac-
tured in accordance with SANS 966
quality standard.
“The increased demand for mPVC
piping systems is due to its applica-
bility for large-bore water infrastruc-
ture projects. It has been designed
specifically to provide similar tensile
strength and greater resilience than
standard PVC piping products. And,
ideally suited to bulk water supply
projects because mPVC is consider-
ably more ductile than industry-
standard unplasticised polyvinyl
chloride (uPVC).
The ductility of mPVC pipe gives
it exceptional resistance to crack
propagation under pressure. In ad-
dition to superior toughness, mPVC
has reduced wall thickness. This
translates into less raw materials
during the manufacturing process,
and ultimately a lighter product
that is easy to transport, install, and
minimises its total carbon footprint.
Managing Director Juan Muller
notes that the manufacture of the
new 630 Class 16 mPVC pipe has
allowed DPI Plastics to make sig-
nificant inroads into the bulk water
infrastructure segment. “In terms
of what is happening in the market
right now, there have been a lot of
large-bore orders coming through.
Government is certainly investing in
major water projects. The building
industry is stagnant at the moment,
but when one looks at infrastructure
and the provision of bulk water, it has
been active for the past eight months
at least, which has been very good for
us,” Muller concludes.
■
PVC piping for infrastructure projects
DPI Plastics has already racked up two major orders for its new
630 mm Class 16 Modified Polyvinyl Chloride (mPVC) pipe for
infrastructure projects.
T
he top accolade recognises the
city’s outstanding work at its
five operational landfill sites
at Rooikraal, Weltevreden, Rietfon-
tein, Simmer and Jack and Platkop.
Ekurhuleni currently collects over one
million tons of waste per annum from
over one million households each
week. Thewaste consists of domestic,
industrial andgardenwaste; asbestos
waste is only accepted at the city’s
Platkop landfill site.
The cornerstone of the city’s main
objective of effective waste manage-
ment includes economic opportuni-
ties, the social impact and the envi-
ronmental benefits.
Receiving the award, Ekurhuleni’s
Member of the Mayoral Committee
Ekurhuleni scoops top
award for waste
management
At the Waste Khoro 2016 conference held in Durban,
the City of Ekurhuleni scooped the top award for the
best managed municipal landfill sites in Gauteng.
(MMC) for Environmental Develop-
ment Portfolio, Ndosi Shongwe
said: “Ekurhuleni’s main focus is on
developing new markets for waste
and diverting waste disposal from
landfill sites. In addition to reducing
the Ekurhuleni’s carbon footprint,
the city aims to create a renewable
energy supply, and to increase job
creation and skills development in
all projects implemented by the city.”
The extraction and utilisation of
landfill gas reduces harmful green-
house gas (GHG) emissions and
prevents explosion hazards at the
landfill sites from the accumulation
of methane gas. Ekurhuleni currently
utilises the landfill gas to generate
1 MWof electricity at the Simmer and
Jack landfill site, which is distributed
directly to the municipal grid, sav-
ing the municipality approximately
R400 000 a month.
Shongwe said the process of
electricity generation is expected to
expand to three more landfill sites.
Since its inception, the project has
reduced emissions by 748 781 tCO
2
e
(tonnes of carbon dioxide equivalent)
to May 2016.
■