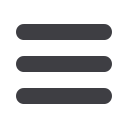

news
Wire & Cable ASIA – September/October 2009
44
❍
Rosendahl RX45 with a ROEX extruder
Advanced crosshead technology
The challenge in distributor design is
to find the optimum dimensions of
the distributor to attain a balanced
flow at the exit. Rosendahl’s distributor
concept is said to guarantee homo-
geneous material flow – independent
of the processed materials and
independent of the output. This opti-
mised material flow provides high
centricity and allows a reduction in
average wall thickness and therefore
reduces the manufacturing costs.
With the help of the latest finite
element simulation programmes,
Rosendahl conducts mechanical cal-
culations and rheological analysis of
its cross-head series.
The simulation also enables analysis
of pressure, temperature rise, velocity,
stress and strain rate distributions
over the entire simulation domain.
Especially when designing the distri-
butor, it is important to adapt the
distributor’s channels to the flow path
of the melt.
In order to offer a broad material
spectra, Rosendahl partnered with
university institutes to research a wide
range of materials for the cable
industry, and now offers a material
database that includes standard as
well as special material (such as
foamed material blends, LSOH or
XLPE).
Rosendahl’s ongoing communication
with polymer manufacturers ensures
that all technology is completely
up to date. Rosendahl, as supplier
of extruders, crossheads and of
complete extrusion lines, is in a
position to investigate and under-
stand the polymer extrusion process.
The integrated simulation results,
together with the experiential data,
have enabled optimisation of the head
design and ultimately to achieve a
high quality of extrudate.
Rosendahl Maschinen – Austria
Fax
: +43 3113 5100 59
:
office@rosendahlaustria.comWebsite
:
www.rosendahlaustria.comJSW Steel Ltd (JSW), located in
Toranagallu in the state of Karnataka
in India, has commissioned the first
eight-strand billet caster on the Indian
subcontinent together with SMS
Concast, Zurich (Switzerland), a com-
pany of the SMS group, Germany. The
billet caster is part of JSW’s expansion
programme which will bring the
production capacity at the Vijayanagar
works to 7million tpy.
The billet caster can be used for open
and submerged casting. It is designed
for a production capacity of 1.7million
ton of billets per year.
The high-speed caster contains the
convex mould technology, electro-
magnetic mould stirring, hydraulic
mould oscillation and the Conseal IV
technology. The production process
is directly tuned to the downstream
wire rod and rebar rolling mills with
hot discharging route.
SMS Concast delivered the auto-
mation software, including level-2
Controlware which is linked to the
level-3 system of the plant.
SMS Concast AG – Switzerland
:
sales@sms-concast.chWebsite
:
www.sms-concast.chSMS Concast AG commissions eight-strand billet caster at JSW
news