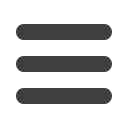

Redefining aggregates production
Weir’s process-focused solution ups CNC Crushers’ output
Rather than sourcing expensive sand and
aggregates on building sites, a start-up
company on the West Rand, Gauteng, South
Africa, has begun a ground breaking new
operation that turns spoils and site rubble into
valuable building materials for re-use on site.
The aptly named Ground Breakers
operation makes use of a portable scalping
and screening machine to separate
excavated materials into different sizes
or streams such as building sand, building
stone, fill, bedding or a range of different
sized aggregates as specified by an engineer.
Rather than excavate a site and pay for
spoils to be dumped, the dynamic duo of
JC Janse van Vuuren and Johan Meintjes
have turned this traditional method around
and are successfully marketing the concept
of processing the spoils on site. In addition
to saving on dumping costs, builders have
the added benefit of reusing the materials
on site and reducing the need for additional
aggregates to be procured.
“The newly available Powerscreen
Warrior 800 scalping screen from ELB
Equipment is easily transportable and can
begin operation in hours of delivery. The
aggressive nature of the screening process
allows large quantities of materials to be
processed quickly and the addition of a
scalping deck ensures that oversized rocks,
rebar or mesh from the building site are
seamlessly separated without impacting
Stilfontein-based sand and aggregate
supplier CNC Crushers raised throughput
at its Roadstone Shaft 5 crushing plant by
45% while cutting back on maintenance
and simultaneously increasing production,
after implementing a full process-focused
solution from Weir Minerals Africa.
According to JD Singleton, Weir Minerals
GM for Trio and Enduron equipment, the
customer was experiencing high wear on the
installed conventional cyclone, as well as on
the older technology pump, having to replace
liners every 120 hours of operation.
“Our brief was to increase solids to
the cyclone underflow and increase the
wear life on the cyclone feed pump,” says
Singleton. “The continuous breakdowns
experienced with the older-technology
crushing equipment, and the excessive oil
usage was also causing high downtime for
the plant. CNC Crushers needed a solution
that would utilise the existing footprint and
infrastructure.”
As a solution, Weir Minerals Africa
installed a new technology Warman WBH
The Powerscreen Warrior 800 scalping screen is performing beyond Ground Breakers’
expectations.
CAPITAL EQUIPMENT NEWS
AUGUST 2017
39
MATERIALS PROCESSING NEWS
100 slurry pump and a Cavex 400CVX10
hydrocyclone; it also replaced the existing
cone crushers with Trio TC51S and TC36SH
cone crushers to increase uptime and reduce
maintenance costs.
“After 1 900 operating hours, the slurry
pump was still running without needing any
replacement parts, a vast
improvement on the pre-
vious mean time between
liner replacements of 120
hours,” he says.
According to CNC owner
Carl Crous, this meant
that the company could
take pumps off the critical
maintenance list. “Pump
problems are something of
the past,” says Crous.
With regard to the
hydrocyclones, these proved
to be more efficient than
the conventional cyclones,
highlighting the benefits of
the Cavex hydrocyclone’s
laminar spiral inlet geometry.
“The Cavex hydrocyclone increased the
mass pull to the underflow, which resulted
in increased production and reduced slimes
to the tailings dam,” he says. “Using new
technology equipment pays.”
b
production,” says Van Vuuren.
Partner and technical expert, Meintjes
explains that once the concept of the
business was finalised, the process of
selecting the right machine was a long one.
The focus shifted from the original plan of
using second-hand machines, after studies
had showed that actual running costs of a
new, supported machine would be roughly
on par with the new one. In addition, the
added flexibility of the new type of machine
was preferable as it opened new avenues of
business being easy-to-transport machine,
scalping capabilities.
“We have long-term goals and needed a
machine that can last as long as these plans
and adapt to our changing requirements.
The Warrior 800 gives us versatility to
operate in a quarry on a 24/7 basis and
build up stockpiles and later get transported
to a construction site to process other
materials. On site, it is easy to set up and
operate with hydraulic folding tail and side
conveyors, rigid feed hopper sides and two
speed tracks that can be used to separate
up to three streams and stockpile them.
b
CNC Crushers’ owner, Carl Crous next to a Cavex 400CVX10
hydrocyclone.