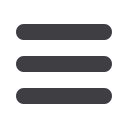

Mechanical Technology — May 2016
27
⎪
Local manufacturing and beneficiation
⎪
adopts state-of-the-art technology
licenses and some cutting edge technol-
ogy that takes all of the guesswork out
of the process.
Trial and error has been replaced with
patented computer-controlled accuracy
and measurement systems that ensure
the precision of each doughnut. ”First,
we enter in the flight parameters into
a CAD program, which will generates
the exact doughnut profile required.
This is transferred to CNC laser cutting
machines, which produce the required
number of identical shapes.
“These are then loaded onto the
pressing machine, which presses the
doughnut to the perfect spiral pro-
file. The pressing loads, over-pressing
distances and maximum speeds are
automatically set based on the flight
size, material specification and section
thickness so that each flight section
manufactured comes out within the
tolerances required,” Bruton explains.”
Operators no longer have to work by
feel and then hit the poorest ones with
a hammer to make them fit,” he adds.
The advantage? “This system enables
us to make augers in 20 mm stainless
steel, for example, and to use harder,
tougher materials such as Hardox and
Benox, which are commonly used on the
mines. It also makes onsite replacement
of individual spares easier, because they
are all accurate.
“Having been manufacturing flights
for over 50 years, we know about almost
every application. We supply fabricators
and distributors across South Africa
and we sell into Zimbabwe, Botswana
and Namibia, among other countries,
to companies servicing mines in Africa.
“In the future, we hope to add another
novel technology called on-edge rolling.
This is used for centreless/shaftless
screws made in thicker material. They
have hollow cores, which are ideal for
sticky or stringy materials.
“Locally manufacturing screws and
flights enables us to offer the best lead
times for custom-made replacement
parts. And we are willing to solve any
flight related problem. If we can’t make
it, we know someone who can,” Bruton
concludes.
q