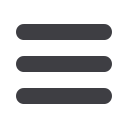

KHS GmbH
Juchostraße 20
D-44143 Dortmund
Deutschland
Tel: +49.231.569 0
info@khs.comVersion 1 Date 29.07.2014
* Subject to technical modifications and price changes. On
request, we will be glad to provide you with a binding offer.
Description
Especially those customers located in hot/tropical regions or with systems
installed in un-air-conditioned bottling shops can experience a significant heat-
up of previously cooled products contained in insulated finished beverage
tanks resulting from prolonged filler downtime. This heat-up leads to increased
pressure in the buffer tank and higher CO2 consumption can be expected due
to the necessity of increasing the pressure of the CO2 cushion in the buffer
tank. This unwanted increase in temperature in the finished beverage tank can
be effectively prevented by cooling the finished beverage in the buffer tank by
means of an additional small heat exchanger in the existing circulation circuit
of existing quality measurement equipment. This effectively prevents the thus
otherwise resulting problem of excessively foaming product at the filler when
the line is restarted.
Benefit
Avoids temperature-related increases in product foaming after prolonged
filler downtime
Avoids quality problems – the beverage temperature is kept at a constant
level
CO2 savings – no additional pressurization of the buffer tank necessary
Reduced CO2 emission to the atmosphere – conservation of resources
Scope of supply
Plate heat exchanger
Circulation line and fittings
Installation of all conversion-related
components
Wiring/piping materials
Modification of the automation,
software and visualization systems
required for operation
Modification of the machine
documentation
Because of different system
configurations, the exact scope of
delivery can be specified only after
review of the current machine
configuration.
Contact
fred.burkat@khs.comKHS Innopro CXC WITH DOUBLE COOLER
EN
KHS Innopro
TECHNICAL UPGRADE
Suitability
For Innopro Paramix/Innopro CX-
type blending and carbonating
systems equipped with beverage
cooling by means of a heat
exchanger and quality
measurement equipment with
product circulation at the buffer
tank.