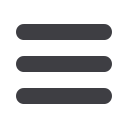

22
Mechanical Technology — April 2016
⎪
Hydraulic and pneumatic systems
⎪
A
ccording to Smith, the “unique,
all-purpose SY pneumatic
manifold valve” is available
in three sizes, namely the
SY3000, SY5000 and SY7000. Thanks
to its innovative redesign and smaller
size, a reduction of 29% is achieved in
installation space offering greater flex-
ibility, increased flow rates and more eco-
nomical operation. Also, the two smaller
valve sizes or the two larger sizes can
be mixed on the same manifold to more
closely match application requirements.
The valve manifold offers piping
options to the top, side or bottom with
various port size options, achieving a flow
rate of up to 1 500
ℓ
/m via the biggest
valve mounted on the manifold.
“The valves in the new SY series offer
further air savings as a result of driving
bigger cylinders with reduced cycle times
Flexible solutions
thanks
to SY manifold valves
Lowering dew point
to protect automation equipment
F
ailure to remove water vapour from
factory air can quickly become a costly
maintenance headache. This accord-
ing to Brian Abbott (right), product manager
at SMC Pneumatics South Africa. “Water
vapour and the resulting water condensate
are the foremost causes of costly downtime
and increased maintenance. The blame is
often laid on the more visible culprit - oil
or contaminants, both of which are easily
removed with proper filtration,” he says.
“Moisture in facility airlines can cause
corrosion and rust which can break loose
to the air passageways causing blockages in
narrow restrictions and filter elements. This
can lead to increased pressure drops and
loss in machine performance, not to mention
energy loss and costs of the compressed air,”
adds Abbott.
Aftercoolers, drip legs and water separa-
tors are used to remove water condensate
from factory compressed air. However, this
air is still at 100% relative humidity and
is, therefore, still at risk of condensing into
water should the surrounding temperature
drop to its dew point.
In order to increase protection of ex-
pensive automation equipment, factory
compressed air must remove as much water
vapour as possible to avoid any condensa-
tion further downstream. Lowering its dew
point does this.
Abbott explains the process: “Drying
compressed air at the highest pressure con-
sistent with the facility’s demands will result
in the most economical dryer operation. For
most industrial applications, the rule is to
first set the pressure dew point to meet gen-
eral requirements, then adjust it to between
-6.0 °C and -10 °C lower than the facility’s
lowest ambient temperature. Hence, factory
air dryness or dew point is relative to the
application specific requirements.
Refrigerated dryers are the most com-
monly used to lower the dew point. A refrig-
erated dryer will further cool the compressed
air by removing heat at its inlet side and low-
ering its dew-point temperature to 3.0 °C,
then expelling the condensate through an
automatic condensate drain. The dryer will
then reheat the dried compressed air back to
ambient temperature by recycling the previ-
ously removed heat using a heat exchange
process. This reheating of the compressed
air to ambient
temperature will
eliminate ‘sweat-
ing’ cold pipes
when working
in humid fac-
tory conditions,”
Abbott explains.
Also recom-
mended is a co-
alescing filter up-
stream from the refrigerated dryer to remove
any compressor oil and other contaminants
that may still be trapped in the compressed
air to ensure the dryer functions properly.
Oil coating the cooling surfaces decreases
efficiency while coalescing filters saturated
with liquid water will aid its drying capac-
ity. In circumstances where factory piping
is exposed to ambient temperatures lower
than the dew point achievable by refriger-
ated drying, alternate methods of drying
must be considered.
Membrane dryers use hollow fibres
composed of a macro-molecular membrane
through which water vapour passes easily,
but it is difficult for air (oxygen and nitrogen)
SMC, a leading provider of pneumatics continues to dazzle with the new
SY series of valve manifolds, which will be manufactured on-site in SMC
South Africa’s new production facilities. Product manager Ernst Smith at
SMC Pneumatics South Africa reveals more.
without the need to use larger, more
expensive solenoid valves. These valves
are available in either rubber or unique
metal seal versions with the metal seal
version being particularly suitable for
higher operating frequencies and ex-
tended lifetime performance – boasting
switching cycles of up to 200-million
cycles,” Smith explains.
The SY series incorporates SMC’s
energy-efficient V100 pilot valve and a
power saving option that reduces power
consumption per valve coil down to just
0,1 W.
The option to have a single valve
mounted on a base is available, if need-
ed, and flow rates exceeding 1 500
ℓ
/m
are also available. The connection to this
plug-in sub-base type valve is via the
well-known M12 waterproof connector.
The valve can be supplied fitted with a re-
sidual pressure release valve that enables
manual dumping of residual compressed
air in the cylinder. This function ensures
safety in the production environment by
avoiding the need to use any external
components or dangerous actions to get
rid of trapped air when the supply pres-
sure is cut-off.
“Safety is always considered when we
look at products and customer applica-
tions,” continues Smith. Overall safety
in applications has been improved in
several ways via optional configurations,
such as:
• The addition of a backpressure check
valve built into the valve or one that
can be retrofitted later.