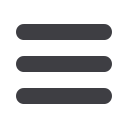

Mechanical Technology — April 2016
35
⎪
Innovative engineering
⎪
Above:
The vertical shaft mucker (VSM): The
use of VSM systems with clamshell muckers
at Venetia is a South African first.
Left:
A view of the Venetia headgears for the
production and service shafts.
Right:
The vertical drill rig (VDR): Murray
& Roberts Cementation has incorporated
mechanised drilling systems underneath the
pre-sink stage.
SA’s shaft sinking specialist
loading system significantly reduces risk
as well as tipping cycle times.
Since Murray & Roberts Cementation’s
pre-sink gantry is rail mounted, on com-
pletion of the first pre-sink operation at
Venetia, it was possible to transport the
entire system on temporary rails to the
position of the second shaft. “For Venetia
we drove the whole set-up, including the
stage and the portal cranes, across to
the new pre-sink site at the mine. The
set up stage for the second pre-sink was
completed inside of five days, a process
that used to take us up to a month,” Du
Plessis reveals.
Turning attention to innovations on
the pre-sink stage itself, the company
has also significantly improved the safety
and effort required for drilling. “We
have incorporated mechanised drilling
systems underneath the pre-sink stage.
The system consists of six vertical drill
rigs supported on swivel arms suspended
underneath the stage. Each operator
guides the drill and manoeuvres it to
match the pattern of holes required for
the blast. An inline pneumatic air leg on
the rock drill extends to create thrust on
the rock drill between the stage and the
floor and, after drilling, for drill retraction.
Much less physical effort is involved and
the operator simply guides the drill’s posi-
tion – and there are no longer any manual
drill operations on the shaft bottom,” Du
Plessis explains.
Also simplified is the shaft lining
process: “Previously, we had to handle
the shuttering and formwork from rigger
mounts drilled into the shaft lining. But
we have now developed proprietary shut-
tering, suspended from the sinking stage.
The shutter depth is 6.0 m, thus after
each 6.0 m of excavation, the shutter
is positioned 12-18 m above the shaft
bottom – and this shutter can be left in
place during drilling and blasting opera-
tions,” says Du Plessis.
The shuttering is suspended from
the lining above using suspension rods,
which remain embedded in the concrete
lining after pouring and protrude through
the shutter at the bottom. To seal the
bottom end of the shutter, scribing sup-
port bars are pushed out towards the
sidewalls, curved scribing planks are laid
and fine steel mesh is used to seal to the
rock interface. A series of steady brackets
between the formwork and rock holds
the shutter securely in place to contain
the self-levelling concrete while it sets.
Air hoist are used to hold the top sec-
tion of the shutter in position in prepara-
tion for concrete pouring. The concrete
is then poured into the shuttering using
concrete kettles, or kibbles, to supply the
concrete from surface. Once the concrete
has settled, the shuttering is ready to
be moved to the next position. The key