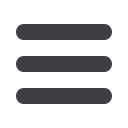

M
arch
2009
www.read-tpt.com10
I
ndustry
N
ews
›
boundary conditions – such as accuracy
of the seam preparation, handling of the
shrinkage process and torch design –
cannot easily be ensured for joining using
one stringer bead per layer.
The second day of the forum began with
an in-depth presentation on ‘Applications,
solutions – implemented projects’. During
the past financial year, in the area of boiler
construction for power plants, Polysoude
has fitted more than 30 made-to-measure
circumferential seam welding systems
for automated TIG welding and several
hundred orbital welding systems for custom
applications.
Following a comprehensive question
and answer session, the perfected,
mechanised welding process was
demonstrated on a rotating part. To
conclude the expert forum, the turnkey
solutions offered by Polysoude for joining
rotors were on display for participants.
A narrow gap welding system for
manufacturing turbine rotors of up to 300
tonnes was set up in the factory hall.
Polysoude will hold a new conference
session for experts in narrow gap welding
in the English language, at the end of
March.
Polysoude
– France
Fax
: +33 240 681 188
:
info@polysoude.comWebsite
:
www.polysoude.compenetration, are x-ray proof, and meet the
highest requirements for metallurgic and
mechanical quality values.
Following the tour, the host and Polysoude’s
CEO, Mr Hans-Peter Mariner, offered an
in-depth insight into the latest developments
in narrow gap welding. This presentation
highlighted that with wall thicknesses of
over 60mmm, welding time is shortened
by a factor of five to ten in comparison
to conventional TIG processes with a
traditional V seam.
The welding characteristics of the parent
material are the decisive factor in the
application of the narrow gap process.
Technical
advances
in
equipment
technology such as automatic centring,
HF-free ignition, seam preparation and
optimised gas protection further increase
the application limits.
The geometry and gap width of the weld
groove are based on the mechanical
properties of the materials being joined,
with the shrinkage characteristics of the
seam being particularly important.
Another key part of the programme was a
presentation on the three different narrow
gap-welding techniques. The first involves
a single pass weld per layer and torch
or workpiece revolution. The second is
dual pass welding next to one another,
when the seam preparation or positioning
exceed the required narrow tolerances of
a few tenths of a millimetre for one stringer
bead per layer.
TIG narrow gap welding with a shuttle-
motion electrode is ideal with very large
wall thicknesses of 150-200mm. This
is particularly the case if the necessary
Polysoude, France, played host to an
expert forum on narrow gap welding from
5-7 November 2008. The successful
event welcomed around one hundred
experts from France, Germany, Austria,
Switzerland, Russia, Hungary and the
Czech Republic.
The event involved two different sessions
in both the French and German languages.
A number of high profile speakers gave
presentations targeted at welding experts
from the high-purity industries, including
food, pharmaceuticals, chemicals, semi-
conductor technology, aerospace and the
onshore/offshore industry.
The power plant construction sector is
currently booming worldwide, with 700
degree power plants the focus of attention.
For plant construction this means using
more pressure-resistant, thick-walled
pipes made from high temperature steels
such as P91 and its successor P92 (X10
CrMoVNb 9-1, WKN 1.4903), conforming
to the ASTM standard (American Society
for Testing Materials).
The key quality features of this new
steel grade are the values for high creep
rupture strength that also apply without
restriction as the benchmark for every
weld seam on these pipes. In particular,
the forum on narrow gap welding
addressed this area of automated
welding technology.
Before the start of the conference
programme, delegates were given a tour
of the factory where P91 pipes (Ø 620mm
and 180mm wall thickness) were joined
using a narrow gap torch in the TIG orbital
welding process using a hot wire additive.
The joined seams offer 100 per cent
Expert forum on narrow gap welding
The expert forum for narrow gap welding – specialists all over Europe were interested in this technology for
the field of energy production and boiler manufacture
In practice – setting of a narrow gap torch on a
P91 pipe (620mm diameter and 180mm wall
thickness)