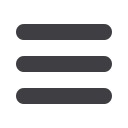

104
›
I
nspection,
M
easuring,
T
esting &
M
arking
M
ay
2009
Pixargus,
Germany,
develops
and
manufactures systems for optical inline
measurement and inspection of plastic and
rubber profiles. The company’s systems
inspect sealing profiles, for example
for the automotive industry, and tubing,
catheters, cables or window seals, as well
as raw material (compounds) made of
thermoplastic elastomers (TPE) and rubber.
The company has launched a new version
of its DualHead System for simultaneous
inspection of the geometry and surface quality
of profiles. The system captures the smallest
irregularities at the surface and minute size
deviations while production is running.
There is a simultaneous inspection of the
surface quality and geometry of profiles,
cables and tubing through an optical inline
process. This provides the possibility
of capturing all relevant geometrical
parameters by a single system. The line
operators can quickly understand any
variations in the production process, and
diagnose the problem and intervene before
out-of-spec material is produced.
The
ProfilControl-DualHead
is
a
combination of one Pixargus surface
inspection system of the ProfilControl-
Surface series and one ProfilControl-
Dimension contour measurement system.
The machine is designed with highly
compact construction.
In addition to the low space requirement,
combining two different Pixargus systems
into one common quality station, provides
another advantage: both systems have
identical, intuitive user interfaces, allowing
operators to quickly become accustomed
to using the two systems. The operator
menu is navigated by large, clearly visible
touchscreen buttons.
Inline surface inspection systems of the
ProfilControl-Surface series detect and
classify defects such as pimples, bubbles,
breakouts, inclusions or holes. Cameras
scan the entire surface, and a ‘surface map’
and individual defect images are displayed
on the touchscreen. During final inspection
it is possible to locate those areas of the
profiles that do not comply with the required
quality standards.
The inline profile measurement systems
are based on the Pixargus ProfilControl-
Dimension series. Cameras arranged
around the profile scan the complete
contour of the extruded profile, and
dedicated software calibrates it against the
contour of a reference profile. The profile
is graphically displayed, complete with its
allowable tolerances.
The sturdy design of the two systems
makes them suitable for the environmental
conditions prevailing at the production
line, and long-life LEDs are used as light
sources.
Pixargus GmbH
– Germany
Fax
: +49 2405 47908 11
:
info@pixargus.deWebsite
:
www.pixargus.deORBIMATIC
Orbital Welding Systems GmbH
Germany
Phone: +49 6408 9026 0
orbimatic@t-online.deORBIMATIC Ireland & UK Office
Phone: +44 1733 555 285
info@orbimatic.co.ukwww. o r b i ma t i c . c om
Next Generation
Orbital Welding
Equipment
ORBIMAT 165 C
A
dvanced
- Single dial operation
- Graphical operator guidance
- Auto programming
BUP Control
sectional control of inside purge pressure
Flow Force
reduces gas filling time of closed weld heads
down to 10 sec
Compatible with all
ORBIMATIC weld heads:
Enclosed
weld heads
Open Arc
weld heads
Tube to tubesheet
weld heads
Inline surface inspection and profile
measurement combined in one system
The ultrasonic weld profile visualisation system
uses phased array technology
The screen shows the nominal and actual
contour of the profile