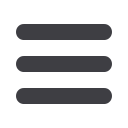

CONTROL SYSTEMS + AUTOMATION
ROUND UP
Compact combi switchboxes with high air output
GEMÜ
, a manufacturer of solutions for
valves, measurement and control systems,
has adapted its range of products in the area
of combi switchboxes.
With the addition of two new product
types and the adaptation of an existing
type, the company completes its product
range and thereby offers its customers
an even more customized selection. This
enables a combi switchbox to be selected
which is even better adapted to specific
requirements.
In comparison to external types, the inte-
grated pilot valve offers both functional and
cost benefits, such as fast reaction times,
automatic programming of end positions
and lower compressed air consumption.
GEMÜ combi switchboxes therefore not
only enable precise position detection,
they also provide efficient activation of the
respective process valve.
With immediate effect, the GEMÜ 4242
combi switchbox is also available with an
increased air output, which means that it is
possible to equip valves with a stroke of 2 to
75 mm with this product.The new size also
comes with the same well-known features.
This includes a high visibility display and
position indicator, various interfaces such as
AS-Interface, DeviceNet, IO-Link and 24V, as
well as fast commissioning using automatic
end position programming, both on-site and
externally. Detailed diagnosis options make
operation easier and simplify fault analysis.
Both new GEMÜ 4240 and GEMÜ 4241
types work with mechanically adjustable
sensors and offer a cost effective alterna-
tive compared to versions with electronic
position detection.
Enquiries: Ivona Jovic.
Georg Venter, Divisional
Manager – Electric Drives and
Controls at Tectra Automation,
pictured with the completed
tailor-made stud press.
Customised stud press solution for automobile manufacturer
TectraAutomation
, part of the Hytec Group, has successfully designed
and fabricated a tailor-made stud press for use inmanufacturing com-
ponents for Ford’s Ford Ranger and Ford Everest vehicle ranges. Com-
missioned for the project byAuto Industrial, the provider of machining
and assembly of various automotive components, the stud press is
used to insert the wheel studs into the front and rear hubs for these
two vehicle types. With no standard stud press on the market that
could meet the customer’s requirements,TectraAutomation was ap-
proached to provide the solution.The stud press is required to press-in
each stud effortlessly using a maximum of 56 kN force and it must
also record an accurate data capture of each press in cycle while
providing a production rate of 175 000 hubs per annum. In addition,
Auto Industrial requested that the press be able to assemble at least
two studs at once while controlling the force and distance travelled
accurately, and the specifications required tight tolerances after as-
sembly. Furthermore, the press was required to performan infrequent
press-out test as part of the quality assurance process.
To achieve these requirements,Tectra Automation designed and
manufactured the stud press frame from the Rexroth range of basic
mechanical elements. “The studs are pressed in using two Rexroth
EMC100XC actuators each driven by a Rexroth MSK060C motor
through standard 20:1 GTM100 gearboxes,” explains Kevin Lombard,
General Manager,Tectra Automation. “A turntable to rotate the hub
is driven by an MSK040C motor through a 20:1 GTE80 gearbox and
control is provided by a Rexroth CML25.1 PLC. Control for the HMI
front-end with onboard PC is enabled by the IndraControl VEP 40.5.
Additionally, we used customised load cells to measure the exact
force and we designed the program to
operate and record the data inhouse.”
Enquiries: Kevin Lombard.
Tel. +27 (0) 11 974 9400 or
Electricity+Control
May ‘17
14