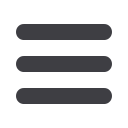
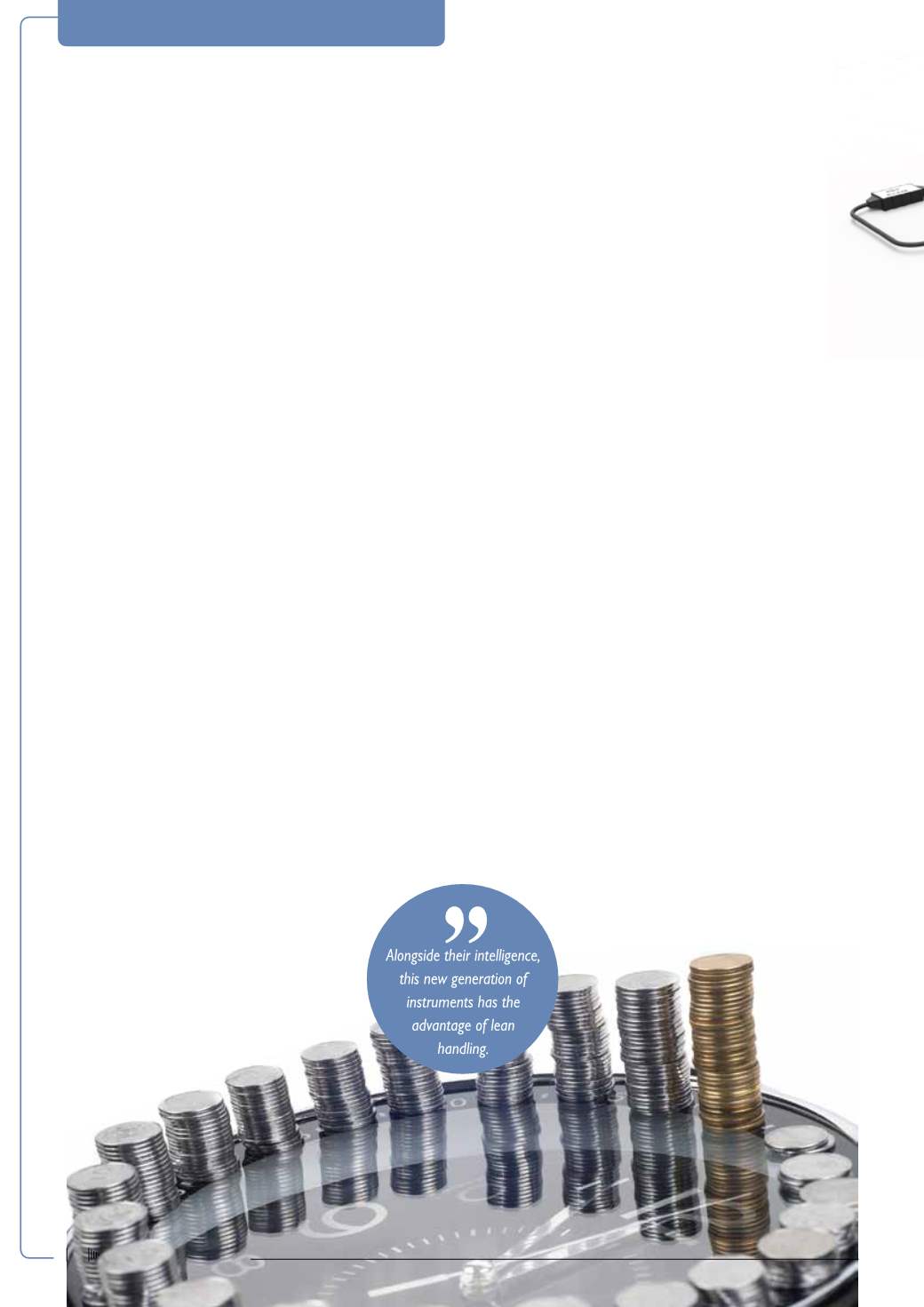
ANALYTICAL INSTRUMENTATION
implementation of a complex PCS, with respect to the cost/benefit
ratio, is often not justified. With process control, along with the de-
mands for increasing quality on the measurement technology to be
used, cost efficiency also comes increasingly to the fore.
Against this background, it is clear that both systemconceptsmust
also be reflected in the sensor technology, in this case in the transmit-
ters. All renowned manufacturers have suitable instruments for each
type in their portfolios. Thus, at the upper end of the performance scale
rank the BUS and HART transmitters, smart transmitters in the middle
and the analogue instruments at the lower end. The latter are losing
more and more ground as technology progresses. They are mainly
being replaced by their digital ‘colleagues’ in the smart category.
The advantages of this change are obvious. Smart transmitters
have similar features as the high-end devices mentioned. However,
despite the high quality of their measurement technology, their prices
are not in the same league and are therefore far more attractive for
less demanding applications.
The cost advantage is primarily achieved through their design,
which does not require complex firmware and consequently leads to a
smaller and therefore lower-cost processor. For smart transmit-
ters, as an example, manufacturer-specific protocols and
the modems suited to them can be used. By using such
non-standard protocols, the connection to the process
Intelligence and Cost Efficiency
=
Smart Transmitters
Jens Baar, WIKA
‘Smart transmitters’ are in a class of their own. With them, the use of the 4-20 mA output signal in process control can be exploited to the maximum.
Alongside their intelligence, this new generation of instruments has the advantage of lean handling. This pays off.
Source 106461124_L_©Lyudmyla V_Fotolia.com
M
any industrial companies have established powerful
Process Control Systems (PCSs) to direct their complex
processes. The PCS collects the data from hundreds upon
hundreds of participants or instruments in the field and carries it to
powerful processors, which then execute extensive control tasks. The
communication between the control systemand the end devices takes
place on the basis of standardised protocols that alongside the core
data such as measured values, provide increasingly more informa-
tion − for example, instrument status and diagnostic information.
For themanagement of data traffic in industrial processes, various
fieldbus protocols have been on the rise for more than a decade. The
widely used HART protocol has by nomeans been outstripped by them
− HART itself continues to experience an increase in demand. Through
the various integration tools for the protocols, configurations can be
made directly from the PCS and information exchanged with the end
devices. In addition to the DD (Device Description) and DTM (Device
Type Manager), ever more frequently these are also software compo-
nents that are based on the new FDT (Field Device Tool) technology.
In addition to the PCS, with increasing central intelligence and ex-
tensive levels of communication, the share of proven systems contin-
ues to grow, which work exclusively with the long-used 4-20
mA output signal and are clearly more straightforward
when compared to a PCS. They offer an alternative for
smaller-size systems or autonomous elements of a
large system in which either the complexity of the
measurement and control tasks is not as extensive
or the processes are less critical. In these cases, the
Electricity+Control
May ‘17
4