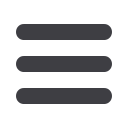

Chemical Technology • August 2015
18
Pump selection
and application guidelines– Part 1
A
pplication limits stated in this article for American
Petroleum Institute (API) and The American Society
of Mechanical Engineers (ASME B73) pumps were
adopted from Process Industry Practice PIPRECP001.
Similarly, some paragraphs in API 610, 10
th
Edition, are
referenced in the sections on Oil Lubrication and Couplings
and Guards. Power recovery turbines and air operated
pumps are excluded from the scope of this guideline.
Selection and application
Centrifugal pumps are widely used in most pumping appli-
cations. By selecting appropriate materials of construction,
speed, size and using available design configurations, cen-
trifugal pumps can be applied in a variety of services includ-
ing toxic, carcinogenic, highly corrosive and abrasive fluids.
Rotary pumps are chosen for special services such as
viscous fluids at fairly constant flowrate and discharge
pressure. The pump internals are lubricated by the pumped
fluid. Most rotary pumps are self priming and can handle
entrained air or gas. In sub-atmospheric suction condi-
tions, entrained gases in the fluid expand, affecting pump
displacement, and thereby reducing its capacity. Rotary
pumps with negative suction pressure require that the pump
casing be filled with liquid to seal internal clearances and
provide lubrication during starting.
Direct acting (steam driven) reciprocating pumps are
suitable for pumping relatively small volumes against high
differential heads. Where process steam is required at dif-
ferent pressure levels, a direct acting reciprocating pump
can be used as a pressure-reducing device to save energy.
Reciprocating pumps can be used to pump a wide variety
of fluids including those with varying corrosive and erosive
qualities.
The centrifugal pump is usually the most preferred con-
figuration in processing industries.
But in certain applications and situations as listed below,
centrifugal pumps may not be appropriate.
• A:
Low flow and high head pumping needs, such as in
chemical injection.
• B:
Fluids containing volatile vapours. Presence of vapours
undermines performance of centrifugal pumps.
• C:
Intermittent services or where a number of liquids of
widely different viscosities are handled.
• D:
Multiple pumping operations including a range of flow
rates and heads.
• E: Constant capacity requirements with varying discharge
pressures.
• F:
Large capacity and high head or low head or low net
positive suction head available (NPSHA) applications.
Performance characteristics of reciprocating pumps make
them an ideal candidate for such applications.
Some of the features, characteristics and limitations that
engineers should consider when selecting a pump are:
• A:
Vertical pumps should be used in those applications
where NPSHA or head/capacity make a horizontal pump
less practical, or in those services (within the operating
A standard set of considerations and best
industry practices that Rotating Equipment
Engineers apply in the selection of various
types of pumps and their auxiliaries, is
described. Typical services and limiting
operating conditions of centrifugal and
positive displacement pumps are included
to aid in the selection process.
by Neetin Ghaisas, ME, PEng, Director of Design Engineering and Rotating Equipment Group
Leader at Fluor Canada, Calgary, Alberta, Canada