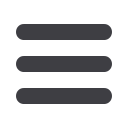

19
Chemical Technology • August 2015
limits stated in this guideline), where a vertical pump
will result in significant savings in plot space, piping and
foundation. It is worth mentioning here that selection
of vertical pump impellers, either open, semi-open or
closed, is governed by the pumping temperature, hydrau-
lic balancing, efficiency, and fluid contaminants.
• B:
High speed vertical in-line pumps can be used instead
of reciprocating pumps for low capacity, high differential
pressure services.
• C:
Proportioning type injection pumps are suitable in acid,
chemical and caustic services. Flow control of pumps can
be achieved by adjusting the stroke.
• D:
Sealless pumps are ideal for handling hazardous
(flammable, corrosive) and highly toxic liquids. Local and
prevailing environmental regulations and risk avoidance
standards may dictate the use of sealless pumps in such
applications. Some pumpmanufacturers offer centrifugal
and rotary pumps, both, in sealless configuration.
• E:
Consider rotary pumps when constant flow over a
wide viscosity or flow proportional to rotational speed is
required. Rotary screw or gear pumps are also preferred
in high viscosity (~ 200 000 cSt) services. But slip in
rotary pumps increases with reducing viscosity which in
turn, affects capacity. Due to small internal running clear-
ances, rotary pumps are not suitable for pumping fluids
which contain suspended abrasive particles.
• F:
Capacity control of reciprocating pumps can be
achieved by regulation of speed, stroke or by both. Some
users specify a bypass line for unloaded startup. Other
designs incorporate mechanical suction valve unload-
ers which are functional until the pump reaches 100 %
speed. Starting against line pressure (such as in multiple
pump applications where they must start against full
line pressure), necessitates a driver with higher start-
ing torque capability. Other options are reduced voltage
starting or use of soft start devices such as fluid coupling.
• G:
Reciprocating pumps are unsuitable when pulsating
flow can not be tolerated, especially if flow and pressure
control instruments are involved. It should be recognised
that pulsations can be damped but the equipment to
achieve pulsation control can be expensive. Options to
look at are rotary or centrifugal pumps because of their
steady discharge pressure and linear flow. Many users
stipulate piping pulsation analysis for reciprocating
pumps with rated power exceeding 100 KW.
• H:
Reciprocating pumps should not be selected when
leakage of pumped fluid must be avoided because of
hazards, such as fire, toxicity, or loss of expensive fluid.
A possible exception is reciprocating diaphragm pumps.
• I:
If ambient temperature is below the pour point of the
pumped fluid, winterisation of pump casing (applies to
spared pumps) and their associated auxiliaries (cooling
water, minimum flow bypass, seal flush, and lube oil lines
and oil filters, etc.) becomes essential.
• J:
Minimum 10 % head rise to shutoff is usually a require-
ment for pumps in parallel operation. It is also important
PUMPS AND VALVES