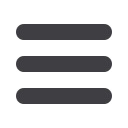

20
J
ANUARY
2017
I NDUS T RY
Growth at UK steel tube specialist
HUB Le Bas is aiming to re-establish
itself as a leading UK precision steel
tube supplier as it enters a new phase
of expansion and capital investment,
building on major client gains over
recent months.
The company, whose roots go back
over a century, has already regained
more than 75 per cent of its client base
since being acquired in December
2015 by global steel and engineering
business Liberty House Group. It
expects to complete this rapid recovery
over the coming months. At present the
company is welcoming almost 50 new
clients per month and has increased its
workforce numbers.
Buoyed by the strength of the come-
back under new management, Hub Le
Bas, which supplies industries as diverse
as automotive, defence, construction
and medical, is now planning to add
two new sites to its existing five-strong
UK network and to invest nearly £2mn
in advanced laser cutting equipment to
further boost quality and productivity.
Rob Sweetnam, managing director of
Hub Le Bas, said, “We are experiencing
a rapid growth in the demand for
precision cut tube components and are
taking the necessary steps to respond
to customer needs. The use of fully
programmed laser cutting equipment
provides clients with improvements in
accuracy and quality while also reducing
downstream assembly costs.”
The new laser cutting machines will
be located in the company’s London,
Manchester and Leicester branches,
supplementing existing capacity at the
firm’s Bilston site in the Midlands.
Hub Le Bas has a portfolio of 8,000
product lines and maintains high stock
levels to meet demand from clients of all
sizes. Staff are equipped to deliver in-
depth product and technical knowledge
as well as high levels of customer
service.
Hub Le Bas
– UK
Website:
www.hublebas.co.ukOrder for reversing cold rolling mill
TALLERES y Aceros SA de CV (Tyasa),
a Mexican steel producer, has awarded
Primetals Technologies an order to
supply a new reversing cold rolling mill
for its production plant in Ixtaczoquitlan.
The cold rolling mill is an element
in Tyasa’s strategy of extending its
portfolio to include flat products, and will
roll 200,000 metric tons of high-strength
and low-carbon steels per year. It is
designed to handle a wide range of end
products, and is particularly suitable for
small batches.
The process equipment and tech-
nology packages not only maintain tight
flatness and thickness tolerances but
also ensure a good quality surface, and
the compact design minimises the pro-
portion of out-of-gauge strip. The project
is due for completion by early 2018.
The reversing cold rolling mill is
designed as a single, four-high stand.
Primetals will supply the complete
process equipment, electrics and
automation from a single source, and will
also be responsible for supervising the
installation and start-up of the plant. The
mill has a maximum roll separating force
of 1,800 metric tons, and will roll strips
with an entry thickness ranging from
0.7 to 2mm down to exit thicknesses of
between 0.3 and 1mm. The strip widths
range from 900 to 1,650mm, and the
maximum coil weight is 32 metric tons.
The scope of supply from Primetals
Technologies includes the rolling
force cylinders – with integrated high-
resolution position transducers, low-
friction seal and guiding rod assembly
– which form the key element in
achieving precise thickness control. The
cylinders and other core components
are manufactured in the company’s own
workshops, and are thoroughly tested
before delivery.
The production of very flats strips is
ensured by advanced work roll bending,
multi-zone cooling of the work rolls and
continuous flatness measurements,
combined with special technology
packages such as automatic flatness
control. For strip blow-off, a special air-
nozzle arrangement is used. The design
ensures efficient blow-off at all rolling
speeds, contributing to a high surface
quality of the rolled strip.
The surface quality is further improved
by using a coil eccentricity compensator
(CECO) model. CECO stabilises the
strip tension and ensures a consistent
strip thickness by compensating for any
eccentricities in the coil that may have
been caused by the clamped head ends
of the strips.
Primetals Technologies Ltd
– UK
Website:
www.primetals.comReversing cold mill from Primetals Technologies. A comparable mill will be installed in the
Ixtaczoquitlan production plant of Tyasa