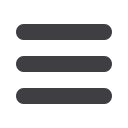

CAPITAL EQUIPMENT NEWS
AUGUST 2016
2
COVER STORY
S
outhern African Hyster customers are
reaping the benefits of aftermarket
initiatives undertaken by Barloworld
Handling and Hyster to enhance lift truck
uptime and productivity and lower their total
cost of ownership.
Building on a successful partnership of
close to 90 years, Barloworld Handling
and Hyster Company are committed to
being much more than lift truck suppliers,
says Boikanyo Mazibuko, deputy CEO
at Barloworld Handling. “In addition to
supplying a full range of warehouse
equipment, IC and electric counterbalanced
trucks, container handlers and reach
stackers, we offer a complete partnership
capable of responding to the full spectrum
of material handling requirements. These
include the highest levels of responsive
aftersales support.”
Mazibuko and other members of the
Barloworld Handling management team
recently visited the Hyster Europe/Middle
East/Africa aftermarket headquarters in
Nijmegen in the Netherlands to ensure the
partnership keeps improving capability and
delivering on its commitment to service
excellence.
On the parts side, this commitment has been
given impetus by Hyster’s state-of-the-art new
Nijmegen automated partswarehouse.“Hyster’s
new parts and accessories programme offers
a convenient and competitively priced source
for Hyster
®
lift truck parts, a complete range
of products with 24/7 access to the on-line
computer network for truck parts identification,
order entry, parts availability checks and back
order status information, and an excellent
first-fill availability and fast parts delivery
available to dealers,” says Mazibuko.
Stocking well over 10 000 line items,
Barloworld Handling already offers local
customers 97% off-the-shelf availability
of fast-moving parts and overnight delivery
to most South African destinations, says
Robin Albany, general manager aftermarket
at Barloworld Handling. “The new Hyster
system speeds up the processing of parts
ordered from Nijmegen, with emergency
orders placed before 14:00 pm now ready
for shipment to Johannesburg by 5:00 am.
Our customers, who often run highly-paced
24/7 operations, are thus able to rely on
faster response times, improving their
productivity and uptime.”
Another focus has been the competitive
pricing of genuine Hyster
®
parts, adds
Albany. “Hyster
®
approved replacement
parts ensure Hyster
®
lift trucks perform as
designed. Supported by Hyster, we are able
to offer our customers genuine parts that
are competitively priced, ensuring not only
robust performance and reliability under
the most demanding conditions, but also
adding to a lower total cost of ownership.”
As an added benefit, local Hyster
®
fleet
owners are now also given access to
Hyster’s Hypass parts service system,
which enables them to check parts
availability at Barloworld Handling and
Hyster worldwide online.
A dedicated parts team at Barloworld
Handling supplies lift truck parts,
attachments and accessories through
regional parts centres around the country.
A parts person is on call 24 hours a day,
seven days a week, including public
holidays, in all major branches.
“The Barloworld Handling sales and
aftersales teams continuously strive to
meet and exceed customer expectations,”
says Mazibuko. “The key differentiator in
our industry is service capability and we are
committed to providing our customers with
some of the best value add in the industry
and proactively assisting them to improve
their productivity and bottom line.”
b
For more information on Barloworld Handling,
its product range and solutions, please
contact your nearest Barloworld Handling
branch, call 0860 HYSTER (497837) toll-free
or visit barloworldhandling.co.za
BARLOWORLD HANDLING AND HYSTER
TAKE PARTS BACKUP TO NEXT LEVEL
Inside Hyster’s state-of-the-art new automated parts warehouse in Nijmegen in the Netherlands.