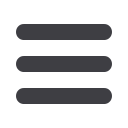

51
CONSTRUCTION WORLD
MARCH
2016
Scania’s P-series provides high-
standard working accommodations
within compact dimensions. For
high-volume payloads and frequent
stops and starts, this series gives drivers both
ample working space and easy cab access.
Aside from reduced weight and extra payload
space, the shorter cab of this series is ideally
suited to congested urban streets and busy
construction sites.
Theuns Naude, Scania South Africa’s
key account manager: construction says,
“The Scania mixer chassis can achieve the
maximum allowed payloads without fear
of overloading with the competitive fuel
consumption edge that Scania is known for.
The feedback from customers is that the
power to mass ratio is very good – and they
are impressed with the driver comfort.” Some
of these customers include the Independent
Group in the Eastern Cape and Nikita
Construction in KwaZulu-Natal. “One metre
cube of wet concrete weighs approximately
2,4 tons, so 6 m
3
will weigh 14,4 tons and
8 m
3
19,2 tons,” explains Naude.
Powerful
“The horse power required for mixers is
normally in a band from 280 to about 400 hp,”
says Naude. Scania’s two models offer 310
and 410 hp respectively. The P310 generates
228 kW and the P410 302 kW.
Because of the Scania modular concept,
the chassis for the mixer models is the same
as its other construction vehicles. “The only
difference is the positioning of the power
take-off (PTO) – it is in a different position and
drives from a 12 o’clock position between the
gearbox and the engine,” explains Naude.
Saving time for bodybuilders
The vehicles arrive in the country with a
factory fitted PTO for the hydraulics. “The
chassis rail is prepared for body brackets –
both flexible and rigid joints – in the correct
position which makes the bodybuilder’s task
easier as it eliminates the ‘guessing factor’,”
says Naude.
There has to be electronic communica-
tion between the chassis and the bodywork
that is fitted. “The electronic functions, such
as the body work communication interface
(BCI control unit), are built in. This control
collects information from the vehicle's
other systems which enables it to evaluate if
activation of different functions is permitted.
The BCI control unit is connected to and
communicates with the other systems in the
vehicle via the vehicle's internal CAN (Control
Area Network).
Meeting quality and warranty
standards
Scania has agreements with various
bodybuilders which stipulate the required
standards needed for bodywork to optimise
the product for a specific function.
“This ensures that the body is fitted
to the chassis in the right way. Once this is
completed Scania does inspections: the
Scania chassis has already been optimised, so
the end product also needs to be optimised
to enable the customer to carry the maximum
payload,” explains Naude.
Driver training is crucial
“Apart from the engines that are already opti-
mised for fuel consumption, we train drivers
of these mixers in their own environments so
that they fully understand the driveability of
the vehicle while they are taught how to use
the unique features. We do onsite training for
drivers as every customer’s operating condi-
tions vary. The driver receives a certification
and is invited back annually for re-training,”
says Naude.
More than selling a
product
As part of the total solution
that Scania customers get,
the operational performance
of the mixer is closely moni-
tored. “We have our 24/7/365
call centre where support
is available immediately.
We also structure unique
repair and maintenance
contracts for the customer,”
says Naude. Part of this
offering is the Scania C200.
This diagnostic system is an
indispensable tool. It fetches
diagnostic information from vehicles in the
field and stores them in a database. This
saves the engineer’s time by not having to
visit every vehicle.
“This system enables the customer to
track his vehicle’s performance and for Scania
to get pre-warnings so that we can inform
the customer. We can then do preventa-
tive repairs before it becomes a problem,”
explains Naude.
A total solution
Naude says that the construction range has a
three year, 450 000 km/5 000 hour warranty.
Year one of the warranty covers the vehicle
bumper to bumper and in year two and three
only the powertrain is covered.
Scania offers in-house finance and
insurance which are tailored around the
customer’s needs. “With the mixer applica-
tion, batching plants are normally in close
proximity to urban areas which ensures that
we have a service centres close by,” says
Naude about the maintenance and servicing
of mixers. “If remote, we can either place
a technician on the customer’s site or we
can bring the mixer to our dealership to
service it there.”
Naude concludes: “We sell the total
package. Driver training, insurance, financing,
servicing, and the Scania C200. The latter
enables the customer to track, repair and
service the mixer and have a high uptime
– which is crucial for mixers as you have
a four hour window between loading and
discharging the concrete.”
TWO
mixer models
Scania South Africa, as
part of their construction
range, offers the local
construction market two
mixer models: the P310 6x4
(which carries a 6 m
3
drum)
and the P410 8x4 (which
carries an 8 m
3
drum).
The 6 m
3
drum is fitted to
a three axle vehicle and
the 8 m
3
drum to a four
axle vehicle.
– complete
SOLUTION
>
Scania’s two models offer 310 and 410 hp
respectively. The P310 generates 228 kW
and the P410 302 kW.